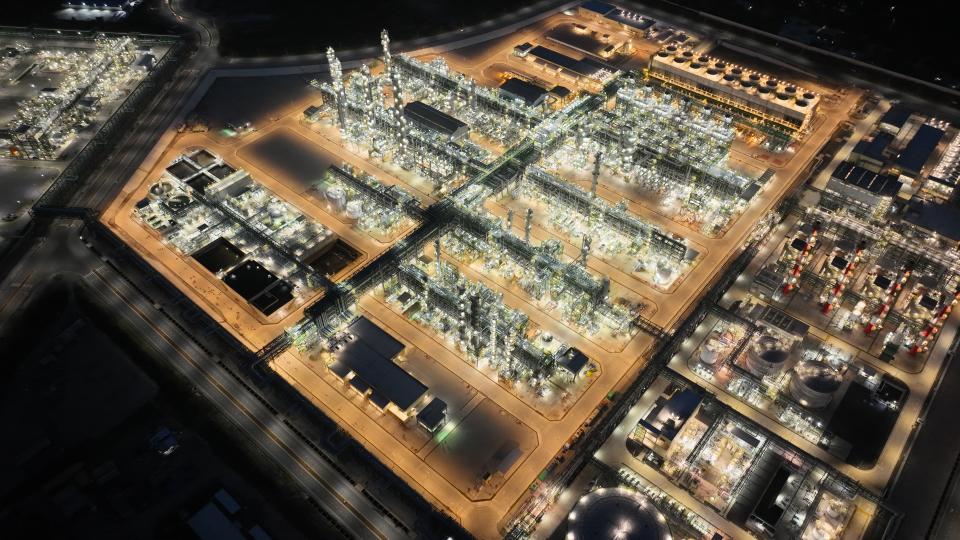
$5.2 Billion Vietnamese Project Records $304 Million Loss in 2024, Continues to Weigh Heavily on SCG’s Financial Results in Early 2025
The Long Son Petrochemical Complex (LSP), Vietnam’s first fully integrated petrochemical facility, has experienced a turbulent launch and operational trajectory since its much-anticipated commercial start-up in late 2024. This article aggregates the latest developments, contextualizes them within broader industry trends, and references previous communications that highlighted both optimism and early warning signs.
Background and Launch
Long Son Petrochemicals Co., Ltd., located in Ba Ria-Vung Tau and wholly owned by Thailand’s SCG Chemicals (a subsidiary of SCG Group), represents a $5.2–5.4 billion investment and is designed to produce 1.55 million tonnes of polyolefins (polyethylene and polypropylene) annually. The complex includes a world-scale, so-called Flex Feed Cracker with a capacity of 998,000 tonnes of ethylene, 500,000 tonnes of propylene, and 101,000 tonnes of butadiene per year, using naphtha, LPG, and soon, ethane as feedstock.
*Data from the Long Son Environmental Permit (in Vietnamese Language) dated August 30, 2023.
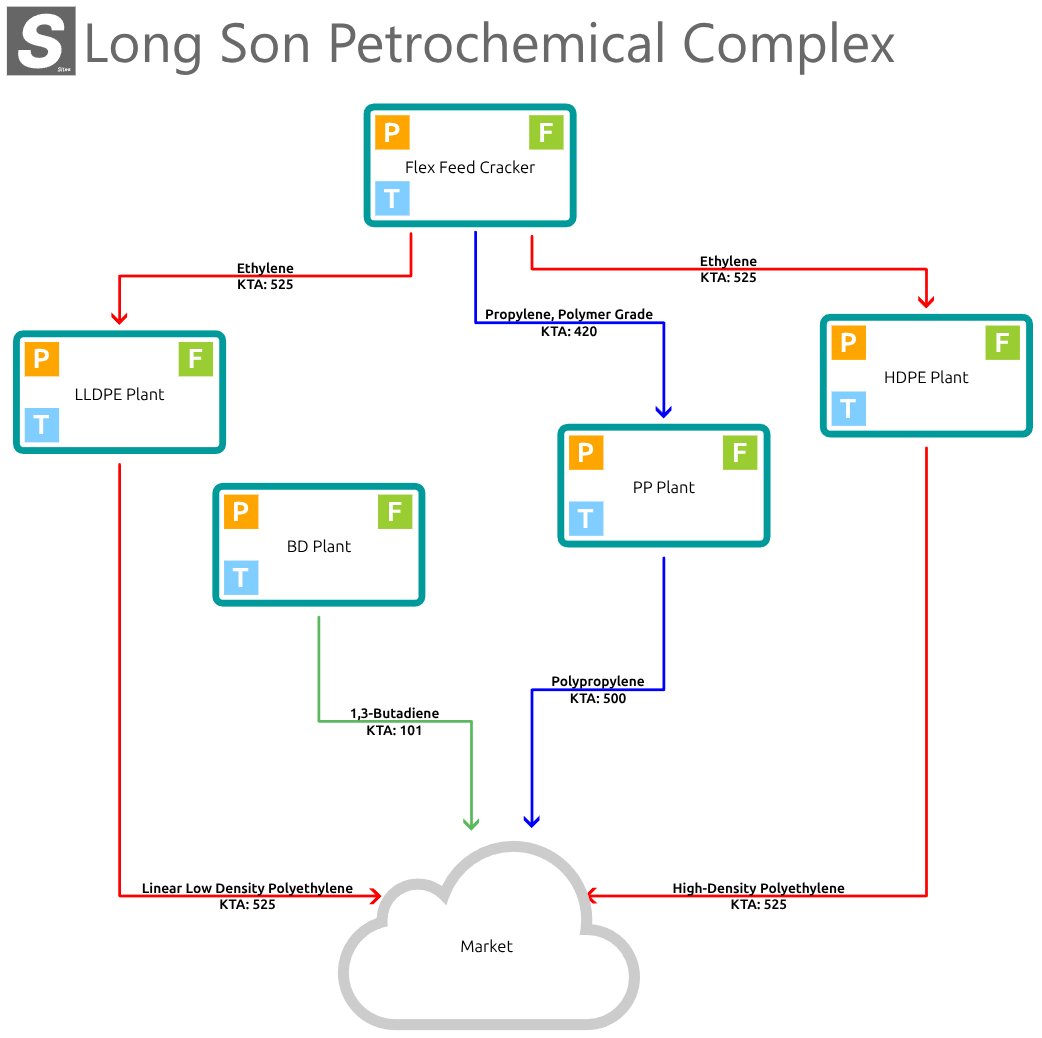
Interactive Process Flow Chart of Long Son Petrochemical Complex based on 2023's Environmental Permit Data | Unique Feature available only on Portfolio Planning PLUS Platform.
After years of construction and trial runs, LSP officially began commercial operations on September 30, 2024. The launch was heralded as a transformative step for Vietnam’s plastics and downstream manufacturing sectors, reducing reliance on imports and boosting local industry competitiveness.
Operational Suspension and Financial Losses
Despite the high-profile start-up, LSP suspended operations in mid-October 2024—just two weeks after commercial production began. This abrupt halt was attributed to:
- High production costs: Naphtha, the primary feedstock, remained expensive amid volatile crude oil prices.
- Weak global demand: A global downturn in the petrochemical market, exacerbated by oversupply and sluggish downstream demand, led to poor product margins.
- Low chemical spread: The spread between naphtha and polyethylene/polypropylene prices dropped to $300–$343 per tonne, below the threshold for profitable operations.
SCG Chemicals reported a staggering loss of $303.6 million from LSP in 2024, with monthly expenses at the complex reaching $35.5 million—40% of which are non-cash items like depreciation. The financial drag from LSP sharply reduced SCG’s consolidated profit, even as its other businesses remained profitable.
Capacity Questions and Technical Details
Our prior communication raised questions about the actual cracker capacity and the interpretation of trial run figures, whereby we issued a mass balancing challenge that still awaits contributions from users of the PPPLUS Platform.
Various data sources have reported diverging plant capacities for both the cracker and the downstream plants. In addition, calculated feedstock requirements to match the reported ethylene and propylene outputs are not making any sense in terms of cracker capacity. The figures we have used to generate the site's mass balance and process flow chart are taken from the Long Son Environmental Permit (in Vietnamese Language) dated August 30, 2023. During the brief operational window, initial output was reported at 74,000 tonnes—well below nameplate, reflecting the ramp-up phase and subsequent shutdown.
Strategic Adjustments and Future Plans
SCG has not abandoned the project. Instead, it is adapting the business model to address structural challenges:
- Feedstock flexibility: LSP is being retrofitted to use imported ethane as a primary feedstock, which offers better margins than naphtha. The company plans to invest an additional $400–700 million to enable the cracker to use up to two-thirds ethane, with completion targeted by end-2027.
- Cost management: SCG is implementing group-wide cost reductions and discontinuing unprofitable businesses, aiming to save 5 billion baht and cut working capital by 10 billion baht by early 2025.
- Potential restart: With recent improvements in polyolefin-to-feedstock spreads (averaging $396/t in April-May 2025), SCG is considering restarting LSP as early as August 2025, contingent on further margin recovery and market stability.

Long Son Petrochemical Complex Assets | Market Intelligence by Portfolio Planning PLUS
Market and Policy Environment
Vietnam’s government has signaled support for LSP’s expansion, promising to streamline procedures and facilitate stable gas imports, including ethane from the U.S.. However, the domestic market remains under pressure from competitive international polyolefin imports and subdued export demand.
Summary on Key Facts and Timeline
- Sep 30, 2024 - Commercial Start-up: Official launch of Vietnam’s first integrated petrochemical complex in Vietnam.
- Mid-Oct 2024 - Suspension of Operations: Halted after two weeks due to poor margins and high costs.
- Full Year 2024 - 2024 Financial Loss: $303.6 million loss from LSP; group profit slashed.
- 2025 - 2027 - Upgrade/Expansion Plans: $400–700 million investment to enable ethane feedstock; expansion under review.
- August 2025 (TBC) - Potential Restart: Dependent on market spreads and demand recovery.
Outlook
The Long Son Petrochemical Complex exemplifies both the promise and pitfalls of mega-projects in volatile global markets. While its technical capabilities and strategic significance remain intact, the project’s near-term viability hinges on market recovery, successful feedstock diversification, and continued government support. SCG’s willingness to invest further and adapt its strategy suggests a long-term commitment, but the road to profitability remains challenging and closely watched by industry observers.
#technipenergies #basf #mitsuichemicals # univation #unipol #hypol #steamcracking #lsp #steamcracker #vietnam #crackerfeedstock #massbalance #longson #scg