ppPLUS: Technologies and more
Go to Homepage to browse companies and process data
ppPLUS-Solutions providing Services and Support
Register creating your own models
Technology
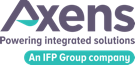
- Name
- Axens MTBE/ETBE
- Owner
-
/ Axens SA - Brand
- Process
- Etherification
- Type
- Etherification of Isoolefins
- Available
-
Process Overview
Axens' MTBE/ETBE technology is a catalytic etherification process that selectively converts isobutylene from C4 hydrocarbon streams into methyl tert-butyl ether (MTBE) or ethyl tert-butyl ether (ETBE) through reaction with methanol or ethanol respectively. The process is designed to produce oxygenated gasoline blending components that enhance octane ratings while reducing vapor pressure and olefin content.
Chemical Reactions
The fundamental etherification reactions are:
-
MTBE formation: CH₃CH₂OH + C₄H₈ → C₅H₁₂O (isobutylene + methanol → MTBE)
-
ETBE formation: C₂H₅OH + C₄H₈ → C₆H₁₄O (isobutylene + ethanol → ETBE)
The reactions are catalyzed by acidic ion-exchange resins in liquid phase under moderate pressure conditions (typically 16-20 bar) to maintain liquid phase operation. The process operates at relatively low temperatures (40-70°C) to favor thermodynamic equilibrium while maintaining sufficient reaction rates.
Process Configuration
The Axens technology utilizes a flexible process design with several key sections:
Main Reaction Section
- Expanded bed reactors or fixed-bed reactors depending on operating requirements
- Multi-stage configuration with interstage cooling for heat management
- Operates at moderate pressure (16-20 bar) and temperature (40-70°C)
- Typically achieves 90-95% isobutylene conversion in the first reaction stage
Catacol™ Reactive Distillation System
- Proprietary reactive distillation technology that combines reaction and separation
- Enables ultra-high conversion rates (>99.9%) by overcoming equilibrium limitations
- Uses conventional catalyst packing without proprietary internals
- Particularly effective for maximizing ether production and isobutylene extinction
Fractionation Section
- Separates unconverted raffinate from ether products
- May incorporate reactive distillation elements for enhanced conversion
- Handles product purification and stream separation
Alcohol Recovery Section
- Raffinate washing column and alcohol recovery for recycle
- Improves overall process selectivity and efficiency
- Optional in ethanol mode due to different phase behavior
Catalyst System
The process utilizes non-proprietary acidic ion-exchange resins as catalysts:
- Sulfonated styrene-divinylbenzene copolymers (macroreticular structure)
- Commercially available from multiple suppliers
- Easy loading and unloading procedures
- High stability under process conditions
Operating Conditions
Typical operating parameters include:
- Temperature: 40-70°C (optimized for equilibrium conversion)
- Pressure: 16-20 bar (to maintain liquid phase)
- Alcohol/isobutylene ratio: 1.0-1.2 (stoichiometric to slight excess)
- Reactor configuration: Adiabatic first stage, followed by lower temperature finishing
Process Performance
According to technical literature, the technology achieves:
- Conversion rates: 90-95% in main reactor, >99.9% with Catacol™ system
- Selectivity: High selectivity toward target ethers with minimal by-product formation
- By-products: Small quantities of tertiary alcohols (TBA), dimers, and water
- Utility consumption: Moderate electrical power (14-20 kWh/t), steam (0.9-1.2 t/t), and cooling water requirements
Technical Considerations
Process Limitations
- Equilibrium constraints: Standard etherification is limited by thermodynamic equilibrium
- Heat management: Exothermic reactions require careful temperature control
- Feed quality: Requires C4 stream preparation to remove dienes and acetylenes
Side Reactions
- Isobutylene hydration to form tertiary butyl alcohol
- Isobutylene dimerization to form trimethylpentenes
- Alcohol dehydration (particularly with ethanol systems)
Process Flexibility
- Switchable between MTBE and ETBE operation modes
- Capable of processing various C4 feedstocks (FCC, steam cracker, dehydrogenation)
- Staged investment possibilities for capacity expansion
- Integration with other Axens technologies for feed preparation
Industrial Implementation
The technology has been commercially deployed in over 30 units worldwide since the 1980s, representing established industrial maturity. The process can be configured for various production capacities and integrated with existing refinery infrastructure for feed preparation and product handling.
References
- Etherification - Axens
- Jan 2011 - Etherification Technologies technical Bulletin - MTBE/ETBE & TAME/TAEE - Axens
- Jack | June 11, 2018 - MTBE/ETBE and TAME/TAEE: Etherification Technologies Process by Axens - Oil & Gas Process Engineering
- Methyl t-Butylether (MTBE) from C4; reaction of methanol and butene; production mix, at plant; 0.74 g/cm3, 88 g/mol. Location: US - United States. Reference year: 2019-2022. Global LCA Data Access
- Dec 2021 - MTBE Production from Isobutylene. Report MTBE E51A Cost Analysis. United States - Intratec
- J.-L. Nocca, P. Travers, A. Koskas | IBP | Conexpo Arpel' 96 - CATACOL™, A LOW COST REACTIVE DISTILLATION TECHNOLOGY FOR ETHER PRODUCTION AND FOR REVAMPING EXISTING UNITS - U.S. Department of Energy (DOE), Office of Scientific and Technical Information (OSTI)
- M. G. Sneesby et al | May 5, 1997. ETBE Synthesis via Reactive Distillation. 1. Steady-State Simulation and Design Aspects. Ind. Eng. Chem. Res. 1997, 36, 5, 1855–1869. DOI: 10.1021/ie960283x
-

No Services yet available.
Enquire in Solutions how we can help you.
Entity | Site (Country) | Asset (Plant) | |||
---|---|---|---|---|---|
![]() |
![]() |
|
MTBE Plant | ||
![]() |
![]() |
|
MTBE Unit |
Content provided by
- Updated by
-
 Kokel, Nicolas
- Updated
- 7/17/2025 10:04 AM
- Added by
-
 Kokel, Nicolas
- Added
- 7/17/2025 8:57 AM
Join ppPLUS to add new content, update or comment.