ppPLUS: Technologies and more
Go to Homepage to browse companies and process data
ppPLUS-Solutions providing Services and Support
Register creating your own models
Technology
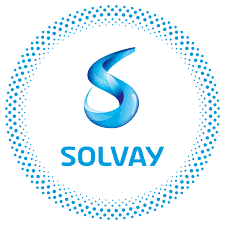
- Name
- Solvay AO Process
- Owner
-
/ Solvay SA - Brand
- Anthraquinone Auto-Oxidation Process
- Process
- Oxidation
- Type
- Riedl-Pfleiderer Process
- Available
-
Technology History
Solvay is a global leader in hydrogen peroxide (H₂O₂) production and has been at the forefront of technological innovations in the anthraquinone auto-oxidation (AO) process since the mid-20th century. Solvay’s proprietary process has evolved through continuous improvement in catalyst design, solvent systems, and plant modularity, enabling the company to operate some of the world’s largest and most efficient H₂O₂ plants. The company’s technology is protected by a series of patents, which details specific process innovations and optimizations.
Technology Summary
The Solvay AO process is a cyclic, continuous method for manufacturing hydrogen peroxide. Its distinguishing features include:
- Use of a proprietary working solution with optimized alkylanthraquinones and a unique solvent blend, enhancing solubility, stability, and hydrogenation rates.
- Modular plant design, allowing scalable capacity and integration with downstream processes (e.g., HPPO units for propylene oxide production).
- Advanced process monitoring and automation, enabling high operational reliability and remote control capabilities.
- Proprietary catalyst formulations and reactor configurations to maximize selectivity and minimize degradation of the working solution.
- Detailed Process Flow and Conditions
1. Hydrogenation
- Reactor Type: Fixed-bed or trickle-bed reactor with proprietary palladium catalyst.
- Working Solution: Contains a blend of alkylanthraquinones (notably 2-ethylanthraquinone and tetrahydro derivatives) dissolved in a proprietary solvent system (e.g., mixtures of aromatic hydrocarbons and polar solvents).
- Conditions: 40–70°C; 2–5 bar H₂ pressure.
- Process Feature: Solvay’s process may employ a “foam-flow” regime, where a self-foaming mixture of working solution and hydrogen gas increases mass transfer and productivity without special foaming equipment. This regime can boost productivity up to six-fold compared to conventional trickle-flow, with minimal loss of anthraquinone.
2. Oxidation
- Reactor Type: Bubble column or packed column.
- Oxidant: Air or pure oxygen.
- Conditions: 30–80°C; atmospheric to 5 bar.
- Process Feature: The hydrogenated working solution is oxidized, regenerating the anthraquinone and producing H₂O₂, which remains dissolved in the organic phase.
3. Extraction
- Unit: Countercurrent extraction columns.
- Solvent: Demineralized water.
- Conditions: 25–40°C.
- Outcome: H₂O₂ is transferred to the aqueous phase, achieving 98%+ recovery efficiency.
4. Purification and Concentration
- Steps: Activated carbon treatment, ion exchange, vacuum distillation.
- Product: Commercial H₂O₂ solutions (35–70 wt%) or electronic grade for semiconductor applications.
5. Working Solution Regeneration
-
Regeneration: Removal of degradation products and water; reactivation of the working solution using proprietary methods and catalysts to maximize cycle life and process efficiency.
Process Efficiency
- Productivity: Foam-flow hydrogenation regime can achieve up to 198 g H₂O₂/h/kg catalyst (vs. 34 g/h/kg in trickle-flow).
- Selectivity: Proprietary working fluid and catalyst minimize loss of active quinone (<1 g/kg H₂O₂ produced).
- Yield: 95%+ conversion of H₂ and O₂ to H₂O₂.
- Energy Efficiency: Modular design and continuous process improvements have reduced both operating and capital costs, with Solvay reporting 70–80% of its capacity in the top 50% of industry cost performance.
Process Economics
- Cost Leadership: Solvay’s process is recognized for its low operating and capital costs, driven by proprietary working fluids, high plant reliability, and economies of scale.
- Sustainability: The process is designed for high resource efficiency and is being further optimized for carbon neutrality, including integration with renewable hydrogen sources.
- Modularity: Plants can be tailored for a range of capacities, from satellite units to mega-scale facilities, supporting both merchant and captive supply models.
Commercial Experience
- Global Footprint: Solvay operates 19 industrial hydrogen peroxide sites and three R&D centers worldwide, making it the world’s largest producer of anthraquinone and hydrogen peroxide.
- Market Segments: The process serves pulp & paper, electronics (ultra-pure H₂O₂), chemicals (HPPO), and environmental markets.
- Track Record: Solvay’s AO process is the backbone of its global H₂O₂ business, with a history of robust cash generation, high EBITDA growth, and continuous investment in process improvement and capacity expansion.
- Innovation: Solvay’s proprietary working fluid and process automation have set industry benchmarks for productivity, reliability, and sustainability.
References
- Hydrogen Peroxide (H₂O₂) - Solvay
- Dominique Vandenberg. GB2334028A. Making hydrogen peroxide by the anthraquinone process. Patent filed: Feb 4, 1998. Solvay SA
- Alain Vandenbussche et al. EP2766299A1. Process for producing hydrogen peroxide. Patent filed: Oct 2, 2012. Solvay SA
- Oct 4, 2022 - Peroxides Webinar - Solvay
- Jun 5, 2025 - Solvay and BASF together reduce scope 3 emissions in hydrogen peroxide production - SOLVAY
- Sara Larson. Master's Thesis 2022: Simulation of a Hydrogen Peroxide Oxidation Tower. Chalmers University of Technology

No Services yet available.
Enquire in Solutions how we can help you.
Entity | Site (Country) | Asset (Plant) | |||
---|---|---|---|---|---|
![]() |
![]() |
|
H202 Import | ||
![]() |
![]() |
|
H202 Plant |
Content provided by
- Updated by
-
 Kokel, Nicolas
- Updated
- 7/14/2025 8:15 PM
- Added by
-
 Kokel, Nicolas
- Added
- 4/4/2022 2:54 PM
Join ppPLUS to add new content, update or comment.