ppPLUS: Technologies and more
Go to Homepage to browse companies and process data
ppPLUS-Solutions providing Services and Support
Register creating your own models
Technology
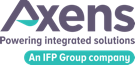
- Name
- Axens Sulfrex
- Owner
-
/ Axens SA - Brand
- Sulfrex™
- Process
- Gas processing
- Type
- Acid Gas Removal
- Available
-
Axens Sulfrex™ is an extractive sweetening process designed to remove sulfur compounds—primarily mercaptans (RSH), hydrogen sulfide (H₂S) and carbonyl sulfide (COS)—from LPG streams. It combines caustic extraction with catalytic oxidation to convert mercaptans into disulfides, yielding a sweetened LPG product that meets stringent sulfur specifications while minimizing equipment and operating costs.
Process Summary
Sulfrex™ sweetens LPG/NGL through a two-step process:
- Caustic Extraction: H₂S is neutralized; mercaptans are absorbed as mercaptides in NaOH (12-15 wt %)
H2S + 2 NaOH → Na2S + 2 H2O
RSH + NaOH → RSNa + H2O
- Catalytic Regeneration: Mercaptides oxidized to disulfides (RSSR) by sulfonated cobalt phthalocyanine catalyst at 38-55°C, regenerating NaOH
2 RSNa + ½ O2 + H2O → RSSR + 2 NaOH
- Phase Separation: Disulfides separated in gravity settler; regenerated caustic recycled
Overall reaction:
4 RSH + O2 → RSSR + 2 H2O
The process is applicable to:
- Olefinic LPG: From FCC, coker, and visbreaking units
- Non-olefinic LPG: From saturated distillation columns and hydrotreating
- Commercial LPG: Meeting specifications for alkylation feedstock and petrochemical applications
Process key features:
- Single-loop caustic balance
- Ambient-temperature operation
- Compact equipment
- >99% mercaptan conversion.
Detailed Process Description
1. Extraction Section
- Feed: LPG/NGL stream at 20-45°C, near atmospheric pressure
- Caustic: 12-15 wt % NaOH (can operate up to 25-40 wt %)
- Column: Counter-current trayed extraction column
- Temperature Control: Above 20°C to avoid caustic entrainment; below 40°C for optimal mercaptan extraction efficiency
2. Oxidation/Regeneration Section
- Catalyst: Sulfonated cobalt phthalocyanine (CoSPc) dissolved in caustic loop at 100 wt ppm
- Conditions: 38-55°C, atmospheric pressure
- Equipment: Air injection system → packed-bed oxidizer → gravity settler
- Mechanism: Mercaptides oxidized via ternary complex formation involving CoSPc, mercaptide anion, and molecular oxygen
3. Temperature Optimization
Based on South Pars Gas Complex operational data:
- Extraction: Optimal temperature 36-37°C for propane, 34-35°C for butane
- Oxidation: Optimal temperature 40-41°C for maximum mercaptide conversion (98.5%)
- Upper Limit: Maximum 55°C to prevent catalyst decomposition and stress corrosion
Process Performance
Metric Value Mercaptan conversio >99% (mercaptide to RSSR) Total sulfur removal 84-97.7% (depending on conditions) Operating temperature (extraction) 20-45°C Operating temperature (oxidation) 38-55°C Pressure Near atmospheric Caustic concentration 12-15 wt % (up to 25-40 wt %) Economic Efficiency
- Low OPEX: Regenerable caustic reduces chemical costs; ambient-temperature operation eliminates heating utilities
- Compact CAPEX: Single-loop design and atmospheric pressure minimize equipment sizes
- Byproduct Value: Disulfides (RSSR) can be sold or processed further
- Mild Conditions: Ambient temperature and pressure reduce infrastructure requirements
Commercial Experience
Axens comments that "85 Sulfrex™ and Sweetn’G™ units are under license" (as of Jul 2025) but does not provide a breakdown by technology. This figure supersedes earlier literature (e.g., 2011 estimates of “over 40 Sulfrex units”).
Major Projects:
- South Pars Gas Complex (Iran, 2003): Phases 9-10 implementation with optimized extraction temperatures of 36-37°C and oxidation at 40-41°C
- PRefChem (South Korea, 2015): Unsaturated LPG extractive sweetening unit upstream of polymer-grade propylene recovery
- Petroperú Talara (Peru, 2025): 8,000 bpd LPG sweetening unit as part of refinery modernization
- Pertamina Balikpapan (Indonesia, 2020): Sulfrex LPG sulfur removal unit
References
- Afshar, Ali S. and Sayed Reza Hashemi. Jul, 29, 2011. Role and Effect of Temperature on LPG Sweetening Process. Int. J. Chem. Mat. Biomol. Sci. ISSN 2415-6620
Vol. 5, No 7, 2011. - Axens SULFREX® Process: LPG, Light Naphtha Treating (Sweetening) Process. Naver Blog, 2018.
- NGL & Condensates sweetening - Axens
- LPG Sweetening & Olefins Recovery - Axens
- Jul 16, 2015 - Axens PR - Axens to supply technologies for S-OIL’s residue upgrading capacity expansion project - Axens
- Nov 9, 2009 - Axens Awarded Modernization Contract for Talara Refinery (Peru) - europétrole
- Oct 6, 2016 - PR - Pertamina Licenses Axens Technologies for its Balikpapan and Cilacap Refineries in Indonesia - Axens
- Caustic Extraction: H₂S is neutralized; mercaptans are absorbed as mercaptides in NaOH (12-15 wt %)

No Services yet available.
Enquire in Solutions how we can help you.
Technology Unit |
---|
Catalyst Tank |
Caustic Pre-Wash |
Dryer |
Extractor |
Heat Exchanger(s) |
Oxidizer |
Separator |
Water-Wash |
Content provided by
- Updated by
-
 Kokel, Nicolas
- Updated
- 7/9/2025 7:13 PM
- Added by
-
 Kokel, Nicolas
- Added
- 7/9/2025 4:42 PM
Join ppPLUS to add new content, update or comment.