ppPLUS: Technologies and more
Go to Homepage to browse companies and process data
ppPLUS-Solutions providing Services and Support
Register creating your own models
Technology
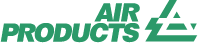
- Name
- Air Products Slurry-Feed Gasification
- Owner
-
/ Air Products - Brand
- Slurry-Feed Gasification Technology
- Process
- Industrial Gas Production
- Type
- Gasification (Syngas Generation)
- Available
-
Introduction: Taxonomy and Technology Heritage
Air Products’ gasification technology combines expertise from two major acquisitions:
- Shell's coal gasification business (acquired in 2018)
- GE’s gasification business (acquired in 2019, including the Texaco process).
This unified platform offers four main technology configurations (Fig. 1), tailored for different feedstocks and applications. The technologies use either dry-feed or slurry-feed systems, each with two syngas cooling options.
Shell’s membrane wall reactor design and multi-burner configuration and GE/Texaco’s refractory-lined reactors form the basis of Air Products Syngas Solutions.
Figure 1 - Air Products' Four Gasification Technology Platforms
Air Products Slurry-Feed Gasification Technology Heritage
Air Products' slurry-feed gasification technology originates from the Texaco Gasification Process (TGP), developed in the 1950s. Acquired by ChevronTexaco and later GE Energy (2004), this technology became part of Air Products' Syngas Solutions™ portfolio in 2019. It complements the dry-feed line-up by offering robust, cost-effective solutions for low-rank coals, petcoke, and refinery residues.
- 1950s: Texaco pioneered slurry-feed gasification for heavy oils at its Montebello pilot plant (California).
- 1978: First coal-gasification demonstration (15 t/d), validating slurry processing for high-ash coals.
- 1984: Commercial deployment at Cool Water IGCC (California), processing coal-water slurry (CWS) for power generation.
- 2004: GE Energy acquired ChevronTexaco’s gasification business, scaling the technology globally.
- 2019: Air Products integrated GE’s slurry portfolio, including 80+ global licenses and China Shenhua JV.
Technology Summary
The slurry-feed gasifier is a single-stage, entrained-flow, refractory-lined reactor operating at:
- Temperature: 1,200–1,480°C
- Pressure: >300 psi (20–69 bar)
- Feed: Coal-water slurry (~65% solids), petcoke, or heavy residues.
- Output: Syngas (CO + H₂) with near-zero liquid byproducts.
Core Innovations:
- Refractory-lined reactor: Handles abrasive feeds without membrane walls.
- Quench/radiant cooling: Flexible heat recovery options.
- Single top-mounted burner: Simplified feed injection.
Feedstock Flexibility
Feedstock Characteristics Examples Coal High-ash, high-sulfur, low-rank coals Illinois No. 6, Lignite Petcoke High-sulfur, low-volatility Delayed coke, fluid coke Residues Asphalt, slurry hydrocracker pitch Refinery bottoms Biomass Torrefied blends (≤20% with coal) Agricultural residues
Detailed Technology DescriptionSlurry-Feed Bottom Quench Configuration
- Feed Preparation:
- Coal/petcoke mixed with water to form pumpable slurry (~65% solids).
- Slurry pressurized to 1,000–1,500 psi and injected via a single top-mounted burner with oxygen.
- Gasification:
- Reactions at 1,200–1,480°C:
C + ½ O2 → CO (exothermic)
C + H2O → CO + H2 (endothermic) - Molten slag forms and flows downward.
- Reactions at 1,200–1,480°C:
- Quenching:
- Syngas and slag enter a water bath at the reactor bottom.
- Slag solidifies into inert granules; syngas cools to <300°C.
- Gas Cleaning:
- Cyclones remove particulates; scrubbers capture chlorides/sulfides.
- Acid gas removal (AGR) extracts H₂S/CO₂.
Advantages: Lower CAPEX, operational simplicity, tolerance for high-ash feeds.
Slurry-Feed Syngas Cooled Configuration
- Reactor: Identical to bottom quench.
- Syngas Cooling:
- Hot syngas exits into a radiant syngas cooler (RSC), generating high-pressure steam (up to 138 bar).
- Syngas then water-scrubbed for final cooling/cleaning.
- Slag Handling: Lock hoppers remove vitrified slag.
Advantages: Higher thermal efficiency (steam export), ideal for chemical complexes.
Applicability
Application Configuration Example Project Output Chemicals Syngas cooled Jiutai MEG (China) 1M t/y ethylene glycol Power (IGCC) Bottom quench Tampa Electric Polk (USA) 250 MW electricity Hydrogen Bottom quench Sarlux IGCC (Italy) Refinery H₂ Liquids (CTL) Syngas cooled Shenhua Ningxia (China) 4M t/y oil products Process Efficiency
- Cold gas efficiency: 76–80% (coal basis).
- Carbon conversion: >99%.
- Oxygen consumption: 380–410 Nm³/1,000 Nm³ syngas.
- Emissions: Near-zero hydrocarbons; sulfur recovered as elemental S.
Process Economics
- Capital costs: 30–50% lower than dry-feed designs.
- Operating costs:
- Refractory replacement every 3–5 years.
- Lower slurry-preparation energy vs. dry-coal grinding.
- Economic drivers:
- Ideal for high-ash feeds and capital-constrained projects.
- Modular scaling (500–3,000 t/d per gasifier).
Commercial Experience
- Global footprint: 80+ licensed plants; 36,000 MWth syngas capacity.
- Key deployments:
- Eastman Chemical (USA): Coal-to-chemicals since 1983.
- Shenhua Ningxia (China): 4,000 t/d coal → 4M t/y liquids.
- Reliability: >90% on-stream factor in chemical applications.
Recent Projects (2020–2025)
- Yankuang Phase II (China, 2023): 2×2,000 t/d slurry gasifiers for methanol-to-olefins.
- Wison Clean Energy (China, 2022): Slurry-fed syngas cooler design for ammonia synthesis.
Technology Outlook
- Waste co-processing: Slurry blends with municipal/plastic waste.
- Carbon capture: Pre-combustion CO₂ capture integration.
- Biomass expansion: 30% torrefied biomass co-gasification tests.
References:
- airproducts.co.uk, Syngas Solutions, information details, solutions referenced therein and brochures available for download, notably:
- 347-18-001-GLB-Mar19-Coal_Gasification-42324.pdf
- 347-18-002-GLB-Mar19-Syngas_Solutions_Offerings-42325.pdf
- 347-18-003-GLB-Aug19-Residue_Gasification-41572.pdf
- US Department of Education (DOE) National Energy Technology Laboratory (NETL), Gasifipedia, NETL: Air Products Slurry Gasifiers.
- airproducts.co.uk, Solid Hydrocarbons: Coal, Petcoke or Biomass via gasification process.
- US Department of Education (DOE) National Energy Technology Laboratory (NETL), Hidayathullah Mohammad, India Gasification 2019 Conference, New Delhi, India, 28-29 November 2019, Air Products Slurry Gasification Technology: Petcoke & Coal.
- ACS, Acetyl Chemicals from Coal Gasification, National Historic Chemical Landmark, Dedicated November 6, 1995, at Eastman Chemical Company in Kingsport, Tennessee.

No Services yet available.
Enquire in Solutions how we can help you.
Title | Date |
---|
Technology Unit |
---|
Content provided by
- Updated by
-
 Kokel, Nicolas
- Updated
- 7/2/2025 8:39 PM
- Added by
-
 Kokel, Nicolas
- Added
- 6/30/2025 6:56 PM
Join ppPLUS to add new content, update or comment.