ppPLUS: Technologies and more
Go to Homepage to browse companies and process data
ppPLUS-Solutions providing Services and Support
Register creating your own models
Technology
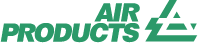
- Name
- Air Products Dry-Feed Gasification
- Owner
-
/ Air Products - Brand
- Dry-Feed Gasification Technology
- Process
- Industrial Gas Production
- Type
- Gasification (Syngas Generation)
- Available
-
Introduction: Taxonomy and Technology Heritage
Air Products’ gasification technology combines expertise from two major acquisitions:
- Shell's coal gasification business (acquired in 2018)
- GE’s gasification business (acquired in 2019, including the Texaco process).
This unified platform offers four main technology configurations (Fig. 1), tailored for different feedstocks and applications. The technologies use either dry-feed or slurry-feed systems, each with two syngas cooling options.
Shell’s membrane wall reactor design and multi-burner configuration and GE/Texaco’s refractory-lined reactors form the basis of Air Products Syngas Solutions.
Figure 1 - Air Products' Four Gasification Technology Platforms
Air Products Dry-Feed Gasification Technology Heritage
Air Products’ dry-feed gasification technology stems from Shell’s coal gasification efforts starting in the 1970s.
Shell developed the technology through pilot and demonstration plants in Europe and the U.S. Notable projects included the Buggenum IGCC plant in the Netherlands, which operated from 1994 until its closure in 2013, and the Shell-Pernis refinery integration, which demonstrated flexible feedstock processing.
When Air Products acquired Shell’s coal gasification business in 2018, it gained access to a portfolio of over 20 operational plants worldwide and extensive intellectual property, securing a proven dry-feed gasification platform.
Technology Summary
Air Products’ dry-feed gasification technology uses a high-pressure, high-temperature gasifier to convert carbon-based feedstocks into clean syngas with over 99% carbon conversion. Operating between 1,300–1,600°C and 350–600 psi (24–41 bar), the process melts mineral matter into liquid slag, avoiding solid ash and producing an inert byproduct that can be used in construction.
Key features include:
- Multiple side burners for flexible and efficient scaling
- A swirl design that effectively separates syngas from slag
- Advanced heat recovery systems to maximize energy use
The gasifier uses a membrane wall reactor design with water/steam-filled tubes instead of traditional refractory linings. This design improves heat management, extends equipment life, reduces maintenance, and allows faster startups without damage from temperature changes.
Feedstock Flexibility and Characteristics
Air Products’ dry-feed gasification technology can handle a wide variety of solid fuels:
- Coal: Processes many types, including high-ash, high-sulfur, and low-rank coals, after drying them to less than 10% moisture.
- Petroleum Coke: Efficiently converts petcoke, a byproduct of oil refining, even when it’s high in carbon and low in volatiles.
- Biomass: Can use torrefied biomass, agricultural residues, and energy crops, either alone or mixed with coal or petcoke.
- Gaseous Feedstocks: Can also process natural gas or refinery off-gases when mixed with oxygen and steam.
- Waste and Alternative Fuels: Capable of converting municipal solid waste, industrial waste, and other alternative carbon sources into valuable syngas, making it suitable for waste-to-energy applications.
The high-temperature, robust design ensures nearly complete conversion of all these feedstocks, including the destruction of organic contaminants.
Detailed Technology Description
Dry-Feed Syngas Cooled Configuration
The dry-feed syngas cooled configuration (Fig. 2) is Air Products’ most thermally efficient gasification option, designed to process solid, liquid, and gaseous feedstocks under high-temperature, high-pressure conditions.
Figure 2 - Dry-Feed Syngas Cooled simplified flow scheme ("Shell Gasification Process")
Feedstock Preparation and Injection:
- Solid fuels (coal, petcoke) are pulverized to 50–200 microns, dried to below 10% moisture, and pneumatically transported with inert gas (recycled syngas or nitrogen) into the gasifier via multiple side burners.
- Gaseous feedstocks (natural gas, refinery off-gases) are injected through dedicated high-velocity ports, pre-mixed with oxygen and steam for rapid, complete conversion.
- Liquid feedstocks (heavy oils, residues) are atomized using steam or nitrogen nozzles and injected tangentially to optimize mixing and prevent wall impingement.
Reactor Design:
- The membrane wall reactor consists of vertical water/steam-filled tubes forming a gastight shell, eliminating refractory linings and enabling superior heat removal and extended operational life (>20 years).
- Multiple burners create a swirling flow that ensures efficient mixing and effective separation of syngas from molten slag.
Gasification Reactions:
- Carbon in solid feedstock partially oxidizes with oxygen and steam to produce carbon monoxide and hydrogen, maximizing syngas yield under sub-stoichiometric oxygen conditions:
- C + ½ O₂ → CO
- C + H₂O → CO + H₂
- Methane in gaseous feedstock undergoes partial oxidation:
- CH₄ + 2 O₂ → CO + 2 H₂
Slag Handling:
- Mineral matter melts into molten slag, flowing down the reactor walls into a water-filled slag bath where it solidifies into inert, vitrified granules suitable for construction or safe disposal.
Syngas Cooling and Cleaning:
- Hot syngas (>1,000°C) is first cooled by direct contact with recycled cold syngas to about 900°C, then passed through a convective cooler to recover high-pressure steam (10–12 MPa) and medium-pressure steam for power and process use.
- The cooled syngas (250–350°C) undergoes particulate removal, scrubbing, and acid gas removal to eliminate contaminants like hydrogen sulfide and carbon dioxide.
This configuration delivers high-quality syngas with excellent thermal efficiency, robust feedstock flexibility, and integrated heat recovery.
Dry-Feed Bottom Quench Configuration
The dry-feed bottom quench configuration (Fig. 3) uses the same feed preparation and membrane wall reactor design as the syngas cooled setup but simplifies syngas cooling by directly quenching hot syngas with water at the reactor bottom.
Figure 3 - Dry-Feed Bottom Quench Configuration ("Shell Gasification Process", 1999)
Legend: a) Preheater, b) Reactor, c) Waste heat boiler, d) Scrubber, e) Quench, f) Extractor, g) Vibrating screen, h) Flash tank, i) Soot-oil tank, j) Homogenizer, k) Naphtha stripper, 1) Naphtha recycle tank.Key Features:
- Direct Water Quench: Hot syngas (>1,300°C) is rapidly cooled to below 300°C by passing through water-filled chambers at the bottom of the reactor. This process also removes slag particles and water-soluble contaminants.
- Simplified Cooling System: Instead of external heat exchangers, a dip tube system circulates quench water, maintaining temperature and quality with heat removal and water makeup.
- Operational Benefits:
- Lower capital costs and faster construction
- Easier operation and maintenance
- Enhanced feedstock flexibility
- Robust performance with fewer high-temperature components
While this configuration is less thermally efficient than the syngas cooled option and produces less high-pressure steam, it is ideal for smaller-scale plants, projects with tight budgets, or where maximum steam recovery isn’t needed. Heat recovery mainly occurs in the membrane wall and from the quench water system.
Applicability and Market Applications
Air Products’ dry-feed gasification technology is used in:
- Power Generation: Enables efficient, low-emission IGCC IGCC power plants.
- Chemical Production: Produces syngas for making methanol, ammonia, and hydrogen—its largest market.
- Hydrogen Production: Creates hydrogen-rich syngas for purification and industrial use.
- Clean Fuels: Supports production of synthetic diesel and jet fuel via Fischer-Tropsch synthesis.
Process Efficiency and Performance
Air Products' dry-feed gasification technology delivers industry-leading performance:
- Cold Gas Efficiency: 82-86% – among the highest conversion rates of feedstock energy to useful syngas
- Carbon Conversion: >99% – minimal carbon loss with near-complete feedstock utilization
- Oxygen Consumption: 380-410 Nm³/1000 Nm³ syngas – efficient stoichiometry reduces operating costs
- Environmental Performance:
- Near-zero liquid byproducts
- No tar formation
- Inert, reusable slag
- Sulfur converted to recoverable H₂S (eliminating SO₂ emissions)
Process Economics and Cost Considerations
Air Products' dry-feed gasification offers compelling economics through:
- Capital Costs: $1,000–1,500/kW for IGCC plants (varies by scale/site)
- Membrane Wall Advantage: 20-year operational life without major maintenance vs. refractory-lined reactors needing replacement every 2–5 years
- Operating Costs: Dominated by feedstock and oxygen; minimized labor/maintenance due to reliability and automation
- Feedstock Flexibility: Enables use of low-cost fuels (e.g., petcoke, waste)
- Scale Benefits: Units handle 750–4,000 tpd; multi-unit plants exceed 10,000 tpd with redundancy
This combination of low lifecycle costs, fuel flexibility, and scalability makes it economically competitive across applications.
Commercial Experience and Deployments
Air Products’ dry-feed gasification technology has over 20 commercial plants worldwide, with more than 500 gasifier-years of proven operation, demonstrating strong reliability and versatility.
Air Products' Lu'an coal gasification project located in Shanxi Province, ChinaKey projects include:
- Jazan IGCC Power Project (Saudi Arabia): Designed to deliver up to 2,110,000 normal cubic metres (Nm3) of syngas per hour by processing vacuum residue and other heavy oil feedstocks supplied from the Jizan refinery.
- Lu’An Clean Energy (China): Four 3,000-ton-per-day gasifiers—the largest dry-feed units at commissioning—forming a $1.5 billion joint venture.
- Pearl GTL (Qatar): The world’s largest gas-to-liquids plant, converting 1.6 billion cubic feet/day of natural gas into 140,000 barrels/day of fuels using syngas cooled dry-feed gasification and Fischer-Tropsch synthesis.
- Jiutai New Material (Inner Mongolia): Coal-to-chemicals (methanol and olefins) project with 5 gasifiers designed to produce over 500,000 Nm3/hr of syngas.
Recent projects focus on integrating renewable energy and carbon capture, supporting the shift to low-carbon solutions.
References
- airproducts.co.uk, Syngas Solutions, information details, solutions referenced therein and brochures available for download, notably:
- 347-18-001-GLB-Mar19-Coal_Gasification-42324.pdf
- 347-18-002-GLB-Mar19-Syngas_Solutions_Offerings-42325.pdf
- 347-18-003-GLB-Aug19-Residue_Gasification-41572.pdf
- Rob van den Berg et al., 30th Sep 2014, The Shell Coal Gasification Process for Reliable Chemicals, Power, and Liquids Production, CORNERSTONE. (retrieved via the webarchive).
- US Department of Education (DOE) National Energy Technology Laboratory (NETL), Gasifipedia, Air Products/Shell Gasifiers.
- CHEManager International, 22nd Apr 2021, Air Products Takes Control of Gasification JV.
- PR Newswire, 5th Nov 2018, Air Products to Acquire GE's Gasification Business and Technology.
- E. V. Vogt and M. J. van der Burgt, 20th Mar 1981, Development of the Shell-Koppers coal gasification process, The Royal Society Publishing, Vol. 300, Issue 1453.
- Green Car Congress, 24th Nov 2010, Study finds that dry-feed gasification for coal-to-liquids is more efficient, lower-emitting and cheaper than slurry-feed; CCS cost-effective for reduction of CO₂.
- MEED, 10th Nov 2011, From gas to end-product at Pearl GTL.
- firstforum.org, 20th World Petroleum Congress, Pearl GTL: Making liquids out of gas on a grand scale. (Document date: 10th May 2012)
- chemwinfo.com, Shell Global Solutions, Coal Gasification factsheet. (Document date: 13th Jan 2018)
- Jerry Kassman, 28th Oct 2020, Presentation: Air Products Syngas for Today - Innovating for a Better Future, Global Syngas Technologies Council (GTCS).
- academia.edu, The Shell Gasification Process (SGP).
- NS Energy, 10th Mar 2021, Jizan Integrated Gasification Combined-Cycle Power Project.
- Mary Bailey, Chemical Engineering, 20th Aug 2018, Air Products to build $650-million syngas facility to supply MEG project in China.

No Services yet available.
Enquire in Solutions how we can help you.
Technology Unit |
---|
Content provided by
- Updated by
-
 Kokel, Nicolas
- Updated
- 7/2/2025 8:21 PM
- Added by
-
 Kokel, Nicolas
- Added
- 6/30/2025 1:46 PM
Join ppPLUS to add new content, update or comment.