ppPLUS: Technologies and more
Go to Homepage to browse companies and process data
ppPLUS-Solutions providing Services and Support
Register creating your own models
Technology
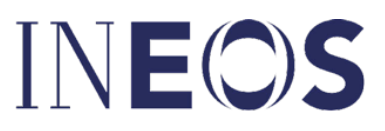
- Name
- INEOS Chlor-Alkali Technology
- Owner
-
/ Ineos Technologies Ltd. - Brand
- BICHLOR™ membrane electrolyser system
- Process
- Decompositions reactions
- Type
- Chlor-Alkali Process
- Available
-
INEOS' chlor-alkali technology is rooted in its BICHLOR™ membrane electrolyser system, a refinement of industrial electrolysis methods developed over 130 years. Here's a detailed technical breakdown:
Core Technology Origins
- Legacy foundation: Inherited infrastructure from ICI's 1897 Weston Point facility (UK), operational for over a century.
- Process evolution: Transitioned from mercury/diaphragm cells (phased out due to environmental concerns) to modern membrane technology.
- Key acquisitions: Expertise consolidated through historical assets, including ICI's electrolysis patents and operational know-how.
Technical Configuration
- Modular membrane cells:
- Each module contains anode/membrane/cathode assemblies in a "zero-gap" design to minimize voltage loss.
- Titanium anode pans with mixed metal oxide (MMO) coatings resist chlorine corrosion.
- Nickel cathode pans with catalytic coatings enhance hydrogen evolution.
- Membrane materials: Fluorinated polymer cation-exchange membranes (e.g., Nafion™ derivatives) enable selective Na⁺ ion transfer.
- Pressure management: Operates at 0–400 mbarg via reinforced pan walls (1mm thickness vs. 0.8mm in competitors).
Performance Metrics
Parameter Specification Energy consumption <1,990 kWh/tonne NaOH @ 6 kA/m² Current density Up to 7 kA/m² Annual NaOH output 52,000–69,000 tonnes per electrolyser Coating lifespan 16 years (cathode), 8–12 years (anode) System lifespan 30+ years with in-house recoating Operational Advantages
- Maintenance efficiency:
- Individual modules replaceable without full shutdowns.
- External headers isolate hydrogen (cathode) and chlorine (anode) streams.
- Safety features:
- Fully wetted membranes prevent gas crossover and explosions.
- Leak-resistant bolted seals on modules.
- Material innovations:
- Explosion-bonded titanium/nickel discs ensure electrical conductivity.
- MMO anode coatings reduce chlorate byproduct formation.
Industrial Process Workflow
1. Brine Purification (ICI Legacy)
- Devices:
2. Brine electrolysis (BICHLOR™ Core):
- Modular cell design (ICI’s bipolar electrolyser patents → INEOS BICHLOR™):
- Anode pan: Titanium substrate with mixed metal oxide (MMO) coating for chlorine evolution
- Cathode pan: Nickel substrate with catalytic coating (16-year lifespan) for hydrogen evolution.
- Cation-exchange membrane: Fluoropolymer-based (e.g., Nafion™) separating anode/cathode chambers.
- Zero-gap configuration: Electrodes pressed directly against the membrane to minimize voltage drop.
- Process flow:
- Purified brine enters anode chamber via feed tubes, fully wetting the membrane.
- DC current (6–7 kA/m²) splits NaCl into Cl₂ (anode) and H₂ + NaOH (cathode):
2NaCl + 2H₂O → Cl₂ + H₂ + 2NaOH - Chlorine gas rises to anode chamber header; hydrogen and 32% NaOH catholyte exit cathode chamber.
3. Gas-Liquid Separation
- Anode side (Cl₂ handling):
- Dechlorination towers: Stripping residual Cl₂ from depleted brine using vacuum or air.
- Coolers/compressors: Chlorine gas cooled to 15–20°C for liquefaction or chemical synthesis.
- Cathode side (H₂/NaOH handling):
4. Product Finishing (ICI/INEOS Methods)
- Chlorine derivatives:
- Caustic soda:
- Crystallizers: Solid NaOH flakes/prills via cooling and drying.
References
- INEOS Group > Electrochemical Solutions > The Chlor-Alkali Process. (Accessed 23rd May 2025)
- INEOS Group > Electrochemical Solutions > Modular Membrane Cell Electrolysers. (Accessed 23rd May 2025)
- INEOS Group > Electrochemical Solutions > INEOS Electrochemical Solutions. (Accessed 23rd May 2025)
- INEOS Group > Electrochemical Solutions > BICHLOR™ ELECTROLYSER brochure. (Accessed 23rd May 2025)
- CloroSur, Technical Seminar, 18th Nov 2014, CHLOR-ALKALI TECHNOLOGY, INEOS Technology.

No Services yet available.
Enquire in Solutions how we can help you.
Content provided by
- Updated by
-
 Kokel, Nicolas
- Updated
- 5/23/2025 9:23 AM
- Added by
-
 Kokel, Nicolas
- Added
- 5/23/2025 7:08 AM
Join ppPLUS to add new content, update or comment.