ppPLUS: Technologies and more
Go to Homepage to browse companies and process data
ppPLUS-Solutions providing Services and Support
Register creating your own models
Technology
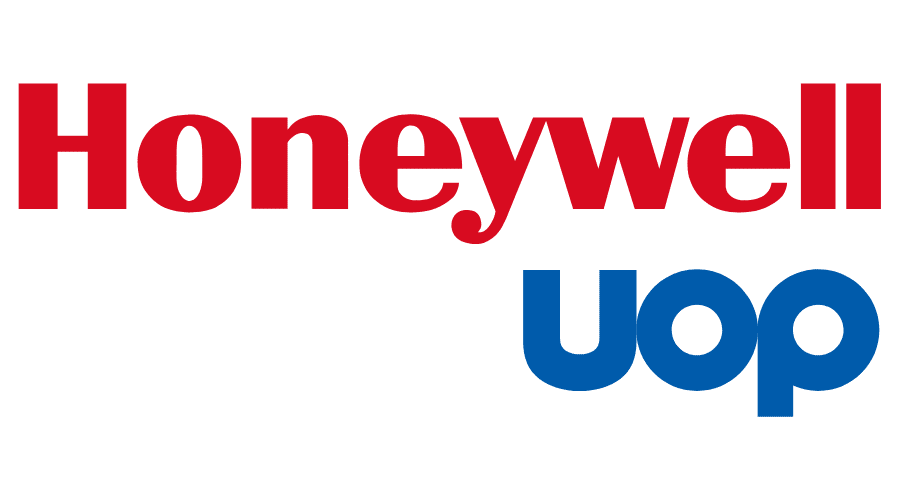
- Name
- UOP Tatoray
- Owner
-
/ Honeywell UOP - Brand
- UOP Tatoray™
- Process
- Dispropornation
- Type
- Aromatics Transalkylation and Dispropornation
- Available
-
Process Summary
The Tatoray process is a technology developed by UOP LLC, a Honeywell company, and Toray Industries Inc. It is used to upgrade toluene, C9, and C10 aromatics through catalytic disproportionation (1a) and (1b) and transalkylation (2) reactions, producing a commercial-grade mix of xylene products and high-purity benzene[1],[2].
Dispropornation reactions[4]
(1a)
(1b)
Transalkylation reactions[4]
(2)
In a modern aromatics complex, this process is integrated between the aromatics extraction and xylene recovery sections of the plant. Extracted toluene is fed to the Tatoray process unit rather than being blended into the gasoline pool or sold for solvent applications[5].
To maximize the production of para-xylene from the complex, the C9 aromatics (A9) byproduct can also be fed to the Tatoray process unit. This shifts the chemical equilibrium from benzene production to xylenes production. Incorporating a Tatoray process unit into an aromatics complex can more than double the yield of para-xylene from a given naphtha feedstock[5].
Process Chemistry
The two major reactions in the Tatoray process are disproportionation and transalklyation. The conversion of toluene into benzene and xylenes (1a) is called toluene disproportionation (TDP). Transalklyation is the conversion of a mixture of toluene and A9 into xylenes (2). The Tatoray process combines both in a single unit[5].
This toluene dispropornation process is designed to function at a high level of conversion per pass. With a typical 50:50 feedstock ratio of toluene and C9 aromatics, the overall conversion is approximately 50% per pass. This high conversion level minimizes the amount of unconverted material that must be recycled back through the BT fractionation section of the complex. A smaller recycle stream minimizes the size of the benzene and toluene columns, the size of the Tatoray process unit, and the utility consumption of all of these units[5].
The Tatoray process reactions are conducted in a hydrogen atmosphere to minimize coke formation on the catalyst. Because there is negligible ring destruction in the Tatoray process, there is very little hydrogen consumption. The methyl groups are highly stable at reaction conditions and are therefore essentially conserved in the reaction. Most of the hydrogen consumption can be attributed to the cracking of the non-aromatic impurities in the feed to the Tatoray process unit[5].
To further increase yields of paraxylene from an aromatics complex -- and allow the use of even heavier feeds -- UOP developed the TA-42 catalyst for the Tatoray process. This catalyst employs a true nano-zeolite which is highly stable, active, and selective because the reactions are controlled by mass transfer. The dimensions of the zeolite pores are smaller, giving it more active sites and greater selectivity to the molecules without getting clogged by heavier C9 and C10 aromatics. As a result of its higher activity, yields of paraxylene per unit of energy – and overall processing capacity -- are higher. The ability to scale up this zeolite was made possible by the invention of a new material[7].
Process Details
The Tatoray process uses a very simple flow scheme consisting of a fixed-bed reactor and a product separation section (Fig. 1). The fresh feed to the Tatoray process unit is combined with hydrogen-rich recycle gas, pre-heated by exchange with the hot reactor effluent, and vaporized in a fired heater where it is raised to reaction temperature. The hot feed vapor goes to the reactor, where it is sent down-flow over a fixed bed of catalyst[5].
Figure 1 - Flowscheme of a TATORAY Process[3]
Process operating conditions are the following[8]:
Total pressure
Temperature
Mole ratio H2/feed
Space velocity
H2 concentration in recycle gas3 MPa (30 kgf/cm2) | 30 atm
400-450 °C
6-10:1
about 1.0 h-1
not less than 70 mol. %The reactor effluent is cooled by exchange with the combined feed, mixed with make-up gas to replace the small amount of hydrogen consumed in the Tatoray process reactor, and then sent to a product separator. Hydrogen-rich gas is taken off the top of the separator and recycled back to the reactor. A small portion of the recycle gas is purged to remove accumulated light ends from the recycle gas loop. Liquid from the bottom of the separator is sent to a stripper column[5].
The C5 overhead from the stripper is cooled and separated into gas and liquid products. The stripper overhead gas is exported to the fuel gas system. The overhead liquid is recycled back to the Platforming™ process unit debutanizer column so that any benzene in this stream may be recovered in the Sulfolane (extraction) unit. The benzene and xylene products, together with the unreacted toluene and A9, are taken from the bottom of the stripper and recycled back to the BT fractionation section of the aromatics complex[5].
Process Performance
A Tatoray process unit is capable of processing feedstocks ranging from 100 wt-% toluene to 100 wt-% A9. The optimal concentration of A9 in the feed is typically 40-60 wt-%. The ability to process A9 makes more feedstock available for xylenes production and dramatically shifts the selectivity of the unit away from benzene (Fig. 2, Table 1)[5].
Figure 2 - Dependencies of benzene, toluene, dimethyl- and trimethylbenzenes contents in equilibrium mixture on aromatic hydrocarbon feed composition[8].
Table 1 - Data of equilibrium mixture composition as a function of feed composition[8].
Equilibrium
mixture
composition,
% molFeed Composition,
% mol Toluene/Trimethylbenzenes (TMBs)Toluene - 100%
TMBs - 0%Toluene - 70%
TMBs - 30%Toluene - 50%
TMBs - 50%Benzene 31.5 8.5 4.5 Toluene 42.0 37.0 21.0 Xylene 22.0 42.0 45.0 Trimethylbenzene 4.5 12.5 29.5 An aromatics complex without a Tatoray process unit can produce approximately 200,000 tonnes per year (t/y) of para-xylene from 25,000 barrel per straight day (b/d) of Light Arabian naphtha (160-300°F cut). If an A7 Tatoray process unit (toluene feed only) is added to the complex, the same amount of naphtha can produce 280,000 t/y of paraxylene, a 40% increase. When an A7/A9 Tatoray process unit is added to the complex, the endpoint of the naphtha is increased from 300 to 340°F in order to maximize the amount of A9 precursors in the feed. The heavier naphtha will produce approximately 420,000 t/y paraxylene – an increase of 110% over the base complex[5].
The Tatoray process produces petrochemical grade benzene and xylenes products. Benzene purity with 100% toluene feed easily meets the ASTM specifications for Refined 545 grade benzene. With a feed of 50% toluene and 50% C9 aromatics, the benzene product purity meets the specifications for Refined 535 grade benzene. The xylene product from a Tatoray process unit contains an equilibrium distribution of xylene isomers and is very low in ethylbenzene (EB). This low EB concentration makes the xylenes produced by the Tatoray process valuable as feedstock to either a Parex™ process or a para-xylene crystallization unit[5].
Economics
The investment cost and utility consumption for a typical Tatoray process unit is shown below. The basis for this case is a unit processing 355,000 t/y (7,700 b/d) of a feed consisting of 60 wt-% toluene and 40 wt-% A9. The investment cost is limited to the Tatoray process unit and stripper column and does not include further downstream
product fractionation. The estimated inside battery limits (ISBL) erected cost for the unit assumes construction on a U.S. Gulf Coast site in 1999[5]:Estimated ISBL Cost,* US Million $ (including initial catalyst and chemical inventories) 11.3 Utility Consumption Electric power, kW
High pressure steam, MT/hr
Cooling water, m3/h
Fuel fired, kcal/hr (millions)341
11.2
478
10*Includes engineering, procurement, erection of equipment on site, and the initial load of TA-4 catalyst.
Commercial Experience
As of May 2015, UOP has licensed nearly 100 aromatics complexes[6], including more than 60 Tatoray units, increasing from 47 Tatoray units as of mid-2001[5].
References
- Brave search summarizer, 4th Jan 2025, Prompt 'Tatoray Toray UOP'.
- toray.jp > Chemical > Inorganic Chemical Products > Major technologies and catalysts. (Accessed 4th Jan 2025)
- Takao Iwamura et al., Toray Industries Inc., 12th Jan 1971, Dispropornation of Toluene, Bulletin of the Japan Petroleum Institute.
- Das, J., Bhat, Y. S., & Halgeri, A. B. (1994). Transalkylation and disproportionation of toluene and C9 aromatics over zeolite beta. Catalysis Letters, 23(1-2), 161–168.
- UOP LLC., 2001, Aromatics & Derivatives, Tatoray™ Process Technical Sheet.
- Joseph Green, 27th May 2015, UOP technology producing petrochemicals, Hydrocarbon Engineering.
- Michael Cleveland, 8th May 2020, Honeywell UOP, New Developments in Catalysts, PTQ Annual Catalysis Supplement.
- SIE NEFTEHIM, LLC, Aromatics Transalkylation and references therein. (accessed 3rd Jan 2024).

No Services yet available.
Enquire in Solutions how we can help you.
Entity | Site (Country) | Asset (Plant) | |||
---|---|---|---|---|---|
![]() |
![]() |
|
DPTA | ||
![]() |
![]() |
|
Xylenes Plant 1 | ||
![]() |
![]() |
|
Xylenes Plant 2 |
Content provided by
- Updated by
-
 Kokel, Nicolas
- Updated
- 1/4/2025 7:18 PM
- Added by
-
 Kokel, Nicolas
- Added
- 11/24/2024 9:34 AM
Join ppPLUS to add new content, update or comment.