ppPLUS: Technologies and more
Go to Homepage to browse companies and process data
ppPLUS-Solutions providing Services and Support
Register creating your own models
Technology
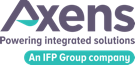
- Name
- Axens H-Oil
- Owner
-
/ Axens SA - Brand
- H-Oil®
- Process
- Cracking
- Type
- Resid Hydrocracking
- Available
-
Process Summary
The H-Oil® Process is a catalytic hydrocracking process, which is used to convert and upgrade petroleum residua such as vacuum resid and heavy oils. Operating H-Oil units have been designed to process a wide variety of feedstocks: atmospheric residues, vacuum residues, and also refractory oils such as heavy deasphalted oils (DAOs), straight-run vacuum gas oils (VGOs), coker heavy gas oil (CHGO) or coal-derived oils such as coal slurries (Direct Coal Liquefaction, DCL), are all potential H-Oil feeds[1],[2].
The H-Oil process is based on the ebullated bed reactor system that was invented in the 1950s. The first patent was issued in 1961. A demonstration plant started up in 1963 at the Cities Service refinery in Louisiana (now CITGO's Lake Charles Refinery) and its successful operation led to the first large scale commercial plant which started up in 1968 at the KNPC Shuaiba refinery in Kuwait[3] (permanently shut down in 1997).
H-Oil aims at metals, sulfur, nitrogen, asphaltenes and Conradson Carbon Residue (CCR) reduction of difficult feeds while maximizing middle-distillate production. However, regardless of the feed, the core principle remains the same. In the H-Oil reactor, liquid feed, hydrogen and catalyst particles are back-mixed. Ebullation of the catalyst bed eliminates plugging, channeling, high pressure drop as well as uneven temperature distribution inevitably encountered in fixed-bed technologies. Stable and continuous catalytic activity is also permitted through fresh catalyst daily addition, thus avoiding time-consuming catalyst renewal operations. Ebullation of the bed is enabled by liquid recirculation, more effective than gas-promoted ebullation and leading to smaller reactor size[2].
H-Oil Base Case
In a base case H-Oil process plant, Arabian Medium vacuum residue (Table 1) is processed. The base case operation is for 65% volume conversion of the 565 °C residue in this feedstock to distillates. This is accomplished using a single train with two H-Oil Reactors in series utilizing second generation catalysts[1].
Table 1 - Arab Medium Vacuum Residue Feedstock Inspection
Cutpoint (°C)
Specific Gravity
API (°)
Sulfur (wt%)
Nitrogen (ppm)
Condradson Carbon Residue (wt%)
Vanadium (ppm)
Nickel (ppm)566
1.037
4.9
5.35
4,380
23.3
132
32
The H-Oil Plant is integrated with an FCC Unit to maximize profitability. The FCC Unit is fed with vacuum gas oil from both the VDU and the H-Oil process. The slurry oil from the FCC Unit can be recycled to the H-Oil Unit for additional conversion to premium fuels . The reactor yields for this plant and fuel oil quality are shown in Table 2[1].Table 2 - Base Case H-Oil Conversion Yields
Spec. wt
(%)vol
(%)Gravity S
(wt%)N
(ppm)V
(ppm)CCR
(wt%)H2S, NH3, H20 5.52 - C1-C3 3.22 - Naphtha (C4-177°C) 8.89 13.10 0.705 0.03 85 Diesel (177-343°C) 18.16 21.95 0.858 0.08 480 VGO (343-566°C) 32.12 36.05 0.924 0.25 1,880 <2 1.3 Bottoms (566°C) 33.98 35.00 1.007 1.24 5.190 63 21.2 Total 101.89 - C4+ 93.15 106.10 0.911 0.56 2.640 23 8.2 Fuel Oil 65.1 70.00 0.964 0.79 3;280 33 11.1
This base case produces[1]:- a relatively high yield (22 vol% on fresh feed) of diesel product, which contains 0.08 wt% sulfur.
- VGO product suitable for feeding directly into an FCC Unit since its hydrogen content is 11.8 wt%.
- unconverted residue that is combined with FCC Light Cycle Oil (0.3 wt% sulfur) to produce a stable, 0.8 wt% sulfur fuel oil with a viscosity of 100 cSt at 50°C.
H-Oil Operations with Lighter/Heavier Feedstock
H-Oil ebullated-bed reactors can operate over a wide range of severity (residence time and temperature) and catalytic activity through adjustments in the type of catalyst and catalyst replacement rate. Plant conversion is higher with lighter crudes and lower with heavier crudes, as shown in Table 3[1].
Table 3 - Operation with Lighter/Heavier Feedstocks
Feedstock Arabian
LightArabian
MediumArabian
HeavyYield of Vacuum Residue (vol%)
Crude Feedrate (BPSD)
H-Oil Plant Feedrate (BPSD)
H-Oil Plant Conversion (vol%)15
160,000
24,000
7519
160,000
30,000
6523
160,000
37,000
55
Lighter Crude ProcessingA lighter crude like Arabian Light will have a lower yield of vacuum residue from the crude unit and less material will be fed to the H-Oil Unit. As a result, the H-Oil Unit would be operated at higher residue conversion (75 vol% versus 65 vol% in the Base Case) while still producing a stable fuel oil product from the unconverted residue. This is due to the lighter feedstock and higher H-Oil Reactor residence time caused by the change in crude type. This operation will result in a higher distillate production rate and less chemical hydrogen consumption per quantity of vacuum residue processed[1].
Alternatively, the refiner could switch on-line to a high conversion catalyst for processing Arabian Light residue and operate the H-Oil Unit at 85 vol% conversion and maximize mid-distillates even more but with some decline in mid-distillate product quality[1].
Heavier Crude Processing
In case of heavier crude like Arabian Heavy, the H-Oil Unit would be fed additional vacuum residue from the crude unit and would operate at a conversion level of 55 vol% which is less than the base value of 65 vol%. This is required in order to maintain reasonable reactor temperatures and hydrogen consumption due to the lower residence time. In this case, the feedstock has become substantially heavier (2.9°API versus 4.9° API for Arabian Medium) and the reactor residence time has decreased due to the higher feedrate[1].
The net effect of the higher H-Oil plant feedrate and the operation at lower residue conversion level would be that the net production of distillates would be nearly the same as in the Base Case but the production of low sulfur residual fuel oil would increase by more than 50 vol%[1].
The overall plant yields and fuel oil production rates relative to Base Case are shown in Table 4[1].
Table 4 - Product Yields with Lighter/Heavier Feedstocks
Feedstock Arabian
LightArabian
MediumArabian
HeavyH-Oil Plant Feedrate (BPSD)
H2 Consumption, (million SCFD)
Product Rate (BPSD)
Naphtha
Diesel
VGO
Bottoms to Fuel Oil
Total
Total Distillates
Fuel Oil S (wt%) / Viscosity @50°C (cSt)24,000
34.1
3,660
6,120
9,950
6,000
25,730
19,730
0.79 / 8030,000
39.3
3,930
6,590
10,800
10,500
31,820
21,320
0.79 / 10037,000
41.8
3,390
6,420
12,350
16,650
38,810
22,160
0.96 / 135
Plant Operating ConditionsThe ebullated bed reactor operates at a constant temperature and catalyst activity. The exotherm generated inside the reactor is quenched by the cold feed and the catalyst activity is controlled by varying the amount and type of catalyst that is added on a daily basis. The conversion of vacuum residue is normally set between 75 wt% and 90 wt% when production of a stable residual fuel oil is desired from the unconverted residue[3].
A comparison of the H-Oil Plant operating conditions with different crudes and variable severity is shown in Table 5[1].
Table 5 - H-Oil Plant Operating Conditions
Feedstock Arabian
LightArabian
MediumArabian
HeavyFeedrate (BPSD)
Catalyst Type (HA / HC)*
Reactor Temperature (°C)
Residue Conversion (vol%)
Desulfurization (wt%)
H2 Consumpt. (Nm3/m3 / SCF/Bbl)24,000
HA
T + 1
75
90
240 / 1,41030,000
HA
T
65
90
221 / 1,31030,000
HC
T + 7
80
80
239 / 1,42037,000
HA
T - 2
55
87
190 / 1,130*HA = High Activity / HC = High Conversion
References
- J.J. Colyar et al., The H-OIL Process: a worldwide Leader in Vacuum Residue Hydroprocessing, CONEXPO ARPEL '96, U.S. Department of Energy, Office of Scientific and Technical Information.
- Axens > Residue Hydroconversion & Hydroprocessing > Ebullated Bed Hydrocracking.
- J. Frecon et al., Axens, Feb 2019, Flexible upgrading of heavy feedstocks, DIGITAL REFINING.

No Services yet available.
Enquire in Solutions how we can help you.
Data provided by
- Updated by
-
 Kokel, Nicolas
- Updated
- 5/4/2025 9:36 AM
- Added by
-
 Kokel, Nicolas
- Added
- 11/15/2022 7:31 PM
Join ppPLUS to add new content, update or comment.