ppPLUS: Technologies and more
Go to Homepage to browse companies and process data
ppPLUS-Solutions providing Services and Support
Register creating your own models
Technology
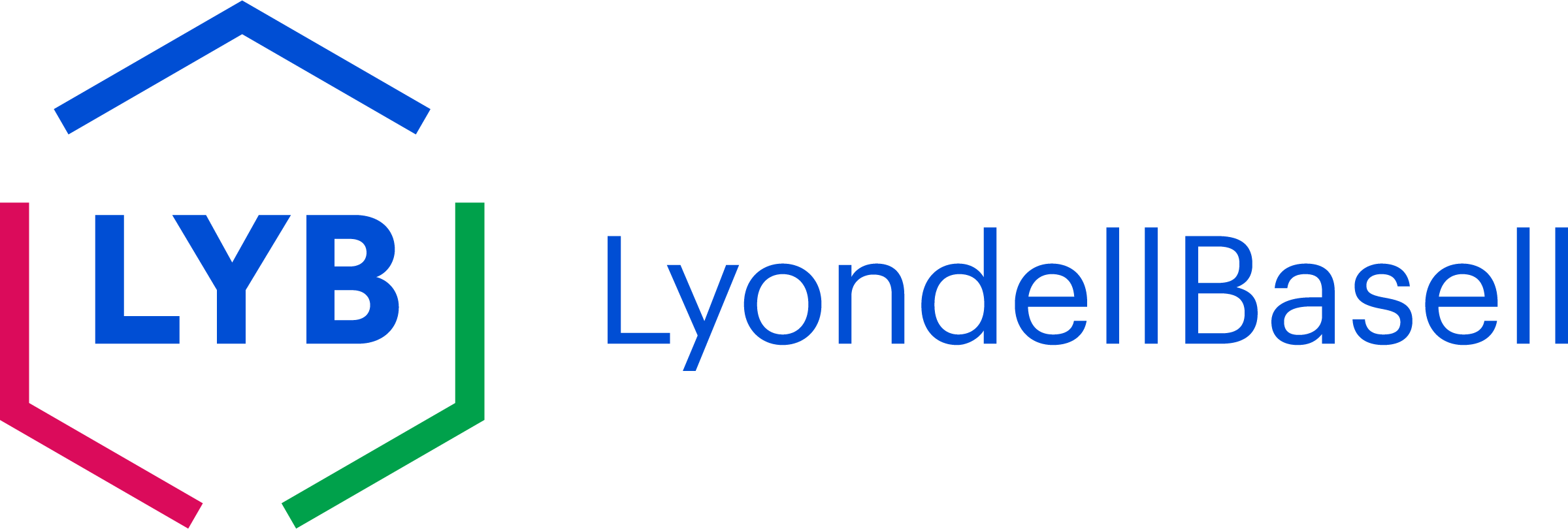
- Name
- Lyondellbasell Spheripol
- Owner
-
/ LyondellBasell Industries N.V. - Brand
- Spheripol
- Process
- Polypropylene processes
- Type
- Bulk-Slurry Polymerization of Propylene
- Available
-
Introduction
Spheripol technology was introduced in 1982 by incorporating breakthroughs in process design with the refinement of gas-phase and bulk polymerization reactors[1].
The Spheripol process is a modular technology. In its most widely adopted configuration, the polymerization section involves the following main Units[2]:
- Catalyst feeding
- Polymerization
- Prepolymerization
- Bulk polymerization (Homopolymer, Random Copolymer and Terpolymer)
- Gas-phase polymerization (Heterophasic Impact and Specialty Copolymer), optional
- Finishing
Technology Generations
In its original design, the Spheripol process comprises one loop and one gas phase reactor (Fig. 1)[1].
Figure 1 - Spheripol simplified process flow diagram[1].
Spheripol 2 or Spheripol II is the latest technology generation that comprises two loop reactors in series (Fig. 2)[3].
Figure 2 - Spheripol II simplified process flow diagram[3].
Process Details
Bulk polymerization employs Jacketed tubular loop reactors completely filled with liquid propylene to produce homopolymer, random copolymer, and terpolymer. The catalyst, liquid propylene, and hydrogen for molecular weight control are fed continuously into the loop reactor. The polymerization reaction is exothermic; the heat of reaction is removed by means of cooling water circulating into the reactor jackets[2].
A homogeneous mixture of porous PP spheres (where active catalyst resides) suspended in liquid propylene is circulated inside the reactor loop by means of a dedicated pump. If the production of random copolymer or terpolymer is desired, ethylene and/or 1-butene are fed – in defined ratio with the plant capacity – into the loop reactor. This process achieves very high solid concentration (at least 50 weight-%) and excellent heat removal (by water circulation in the reactor Jacket) and temperature control (no hot spots). The resulting polymer is discharged continuously from the reactor into a first-stage degassing vessel. Unreacted propylene is recovered, condensed, and pumped back into the loop reactor[2].
For the production of impact copolymers, the obtained polymer is fed to a gas-phase fluidized-bed reactor (FBR) that operates in series with the loop reactor(s). (This gas-phase reactor can be bypassed when homopolymer or random copolymer is produced.) In this reactor, an elastomer (ethylene/propylene rubber) polymerizes within the homopolymer matrix that resulted from the first reaction stage. The carefully developed pores inside the homopolymer particle allow the rubber phase to grow inside without showing the sticky nature of the rubber to upset operations by forming agglomerates[2].
Polymer discharged from the reactors flows to a low-pressure separator and subsequently to a steam treatment vessel where catalyst residues are neutralized and the dissolved monomer is removed, recovered, and recycled back to the reactor system[2].
From the steamer, polymer is discharged into a small fluidized-bed dryer with a hot nitrogen closed-loop system to remove the moisture. The final product is conveyed to an extrusion unit, where it is mixed with additives and extruded to pellets[2].
References
- HMC Polymers, 12th Jan 2022, Spheripol Technology Description Leaflet.
- Spheripol PP, JAM POLYPROPYLENE CO., retrieved from the Internet Archive, 06th May 2018.
- Xiong Wang et al., Versatile Polypropylene Copolymers from a Pilot-Scale Spheripol II Process, Polymers, 2020, 12(4), 751.

Data provided by
- Updated by
-
 Kokel, Nicolas
- Updated
- 6/9/2025 8:01 AM
- Added by
-
 Kokel, Nicolas
- Added
- 11/12/2022 6:14 PM
Join ppPLUS to add new content, update or comment.