ppPLUS: Technologies and more
Go to Homepage to browse companies and process data
ppPLUS-Solutions providing Services and Support
Register creating your own models
Technology
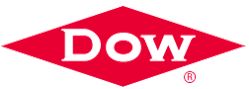
- Name
- Dow METEOR HEXTEO
- Owner
-
/ Dow Incorporated - Brand
- METEOR™ HEXTEO
- Process
- Oxidation
- Type
- Ethylene Oxidation into Ethylene Oxide
- Available
-
Process Summary
The Dow’s METEOR™ EO/EG technology is designed to produce purified Ethylene Oxide (EO), Ethylene Glycol (EG) or purified EO and EG as an integrated process. The METEOR™ Process, which stands for the Most Effective Technology for Ethylene Oxide Reaction[1], is a technology that was first commercialized in 1994 by Union Carbide Corp[2]. Dow’s EO-only process, referred to as the METEOR™ HEXTEO Process, for making EO Derivatives helps customers recover over 99% of the EO produced in their reactor as high-purity EO[1]. EO, for this process, is produced through the conventional EO technology, using a proprietary Silver-based, promoted catalyst[3]. Ethylene conversion is 8 to 13% and EO selectivity is 89%[3].
Process Details
In the METEOR™ Process, ethylene and oxygen are mixed with methane-ballast recycle gas and passed through a single-train, multitubular catalytic reactor ① to selectively produce EO[2].
Heat generated by the reaction is removed and recovered by the direct boiling of water to generate steam on the shell side of the reactor. Heat is recovered from the reactor outlet gas before it enters the EO absorber ② where EO is scrubbed from the gas by water. The EO-containing water from the EO absorber is concentrated. Some impurities are removed by stripping and is then immediately reabsorbed in water ③, thus minimizing the handling of concentrated EO. The cycle gas exiting the absorber is fed to the CO2 removal section ④,⑤ where CO2, which is co-produced in the EO reactor, is removed via activated, hot potassium carbonate treatment. The CO2 lean cycle gas is recycled by compression back to the EO reactor[2].
Most EO plants are integrated with glycol production facilities. When producing glycols, the reabsorbed EO stream ③ is suitable for feeding directly to a METEOR™ glycol process. When EO is the desired final product, the EO stream ③ can be fed to a single purification column to produce high-purity EO. This process is extremely flexible and can provide the full range of product mix between glycols and purified EO[2].
EO Process Catalyst
Dow developed the METEOR™ EO-RETRO 2000 catalyst, which DOW claims to increase the performance and reliability of the EO production process while helping to reduce energy consumption and CO2 emissions[4].
References
- DOW Process Licensing and Catalysts for Chemical Manufacturing, EO/EG Production, Dow’s METEOR™ EO/EG technology (accessed 4th Oct 2024).
- Bee, 5th Jun 2018, Ethylene Oxide Process by Union Carbide Corp, Hydrocarbon Processing (retrieved via the Web Archive).
- S&P Global, Sep 2009, Ethylene Glycol, Process Economics Program Report 2I.
- DOW Case Study, Form No. 878-00116-0221 BBI, 2021: Enabling More Efficient Ethylene Oxide Production: METEOR™ EO-RETRO 2000 Catalyst.

No Services yet available.
Enquire in Solutions how we can help you.
Technology Unit |
---|
CO2 Removal |
EO Absorber |
EO Purification |
EO Stripper |
Heat Exchanger |
Oxidation Reactor |
Content provided by
- Updated by
-
 Kokel, Nicolas
- Updated
- 10/6/2024 3:28 PM
- Added by
-
 Kokel, Nicolas
- Added
- 3/6/2022 7:14 AM
Join ppPLUS to add new content, update or comment.