ppPLUS: Technologies and more
Go to Homepage to browse companies and process data
ppPLUS-Solutions providing Services and Support
Register creating your own models
Technology
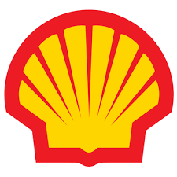
- Name
- Shell EO
- Owner
-
/ Shell PLC - Brand
- EO Process
- Process
- Oxidation
- Type
- Ethylene Oxidation into Ethylene Oxide
- Available
-
Process Background and Early History of EO Catalysts
Ethylene Oxide (EO) is produced by reacting ethylene with oxygen over a silver-based catalyst. These EO catalysts are characterised by several performance factors, including selectivity, activity, productivity and stability. One of the most important measures of an EO catalyst’s performance is its selectivity, which is the ratio of ethylene converted to EO to the total amount of ethylene reacted[1].
In the early days of EO production, the typical start-of-cycle selectivity for EO catalysts ranged from 68 to 70%, i.e., 30% or more of the ethylene feed to the process was lost to the complete combustion side reaction. Then, in 1971, Shell identified an improvement to the catalyst formulation that helped to boost catalyst selectivity to over 80%. Over the next 15 years, the selectivity of EO catalysts seemingly plateaued, with only minor improvements to selectivity performance being realised. Since then, however, there has been continuous improvements for EO catalyst performance, including substantial increases in catalyst selectivity, stability and productivity[1].
Process Description
As per Fig. 1, the EO production divided into four sections: ① Direct oxidation of ethylene; ② EO recovery; ③ carbone dioxide (CO2) removal; ④ Non-condensables removal and EO purification[2].
Figure 1 - SHELL EO Production Process from Ethylene[2].
① Direct oxidation of ethylene:
Producing EO over a catalyst is the first step in the overall EO/EG manufacturing process. Ethylene and oxygen ( supplied from an oxygen separation unit) are fed to an isothermal, multi-tubular reactor, forming EO, by catalysed, direct partial oxidation of ethylene with oxygen. This exothermic reaction occurs in the gaseous phase with the use of a silver oxide catalyst supported on alumina[1-3]:
C2H4 + ½ O2 → C2H4O
The exothermic reaction is carried out under temperatures of 200-300°C, at a pressure of 15-25 bar and a residence time of 1 second. The excess heat is used to produce steam for the process. Another exothermic reaction that takes place is the complete oxidation of ethylene to form CO2 and water The reaction is moderated/optimised using an organic chloride[1,2]:
C2H4 + 3 O2 → 2 CO2 + 2 H2OAs the temperature increases the complete oxidation reaction is favored and the selectivity for the EO process decreases. Therefore, it is important to control the temperature so that complete oxidation is minimized. Selectivity to EO reaches 80-90% if the ethylene conversion is at 7-15%. The excess heat is recovered with coolant for low pressure steam production and is used to offset the later energy demand for dewatering and separation of ethylene glycols[2].
② EO recovery[1-3]:
- The gas from the reactor (containing EO and other constituents) is routed to the EO scrubber for lights removal by water quenching.
- The EO solution from the EO scrubber is concentrated in the desorber and the top stream (crude EO mixture) sent to the purification section made of a stripping column and EO distillation column.
- The bottom water stream from the desorber is cooled and returned to EO scrubber.
- The glycol bleed stream from the EO desorber is further processed.
③ CO2 removal:
- Off-gas from the EO scrubber is sent to the CO2 scrubber and desorber, where CO2 is stripped from the stream.
- The rest of the recycle gas is returned to the oxidation reactor with an addition of the required amounts of O2 and ethylene.
- Some of the recycle gas (0.1 – 0.2 vol%) which contains approximately 70% hydrocarbons (mostly ethylene/methane), is vented and combustedl[2].
④ Non-condensables removal and EO purification[1-3]:
- The crude EO mixture from the desorber enters the stripping column and traces of CO2, nitrogen, methane, ethylene, and aldehydes are removed and join the recycle gas loop to the reactor. Since the recycled gases are rich in ethylene, the process yield and economics can be improved by their recycling.
- The purified EO and water stream recovered from the bottom of the EO stripper enters a distillation column for recovery of high-purity EO (PEO) that is obtained in the top stream. EO is used as a raw material for further processing into specialty chemicals.
- The purified EO/water can be sent to the EO direct hydrolysis section where EO is converted into glycols.
System Design and Reactor Process Options
Depending on the type of catalyst (High Selectivity or High Performance as described in the next section) and on the overall plant capacity target, the HP process enables 30% fewer reactor tubes, 20% shorter catalyst bed lengths and significantly higher work rates. Consequently, the reactor volume can be roughly halved, meaning the elimination of one reactor from the line-up (Fig. 2)[1].
Figure 2 - A reactor can be eliminated from the line-up for certain capacity ranges with the HP process.High Selectivity Catalysts
In 1986, Shell introduced a new generation of EO catalyst in the market: HS catalysts. With these catalysts the initial selectivity values increased by more than six percentage points to give start-of-cycle selectivity values of 86% or higher. Although HS catalysts provided higher selectiviy, their activity and stability were lower compared with traditional catalysts, so they had to be changed out more frequently, with a life of approximately half that of traditional that of traditional EO catalysts that were changed out after three to four years of service[1].
Over time, both process and catalyst improvements extended the life and selectivity of HS catalysts. On the process side, new plants were designed with less-severe operating conditions in order to cope with HS catalysts’ lower inherent activity. Most notably, the new designs were based on lower volumetric production rates (referred to as the catalyst work rate) and lower reactor inlet carbon dioxide concentrations. On the catalyst side, incremental advances in HS catalyst development led to initial selectivities of 90% or more, and greater stability[1].
Consequently, by the turn of the century, new plants were benefiting from excellent selectivity and achieving a catalyst life of three years or more. However, these benefits came with a compromise: increased capital costs. Larger reactors were necessary to compensate for the lower catalyst work rate and larger CO2 removal units were installed to achieve low inlet CO2 concentrations, both of which resulted in increased capital requirements. As the size of the new world-scale EO production plants increased, the associated reactors became a significant capital (equipment) cost[1].
In the 2010, CRI Catalyst Company (now part of Shell Catalysts & Technologies) performed technology improvements that led to new technologies that significantly inhibit catalyst ageing and resulted in the HP catalyst family. HP catalysts are characterised by a high initial selectivity (comparable to that of HS catalysts), but with a significantly slower performance decline, able to operate at significantly higher work rates and to be tolerant of higher CO2 concentrations (Fig. 3)[1].
Figure 3 - Example of selectivity curves comparing HS and HP catalysts over their lives at the same operating conditions.[3].
Energy and Material Flows
Energy and Material Flows of the Ethylene Oxide and Ethylene Glycols processes in Mordijk, The Netherlands, are presented in Table 1[2]:
Table 1 - Energy and Material Flows of the SHELL EO/EG Process in Mordijk, The Netherland.
Ethylene Oxide Mass (kt/year) Energy (pJ/y) INPUTS Ethylene 218 Oxygen 276 OUTPUTS Ethylene Oxide 305 CO2 (partly exported) 75 ENERGY Steam net export -1.5 Electricity 0.31 ETHYLENE GLYCOLS INPUTS Ethylene Oxide 122 OUTPUTS Ethylene Glycols 155 ENERGY Steam 0.7 Electricity 0.04 Fuel Gas 3 0.1 CO2 9 Total CO2 85 Process Licensing
Shell has issued licenses for 89 EO/EG plants worldwide, 53 of which are still operating. Shell claims that nearly 40% of the world’s EO is produced in Shell-licensed and designed plants and that more than 50% of the world’s EO is made using Shell Catalysts & Technologies’ catalysts[4].
References
- Shell Catalysts & Technologies, 22nd Mar 2021, ENHANCEMENTS IN ETHYLENE OXIDE/ETHYLENE GLYCOL MANUFACTURING TECHNOLOGY WHITE PAPER.
- Louise Wong, Ton van Dril, 9th Nov 2020, Decarbonisation Options for Large Volume Chemicals OProduction, Shell Mordijk, PBL Netherlands Assessment Agency.
- a. Scott Jenkins, Content supplied by Intratec Solutions LLC, 1st Oct 2015, Ethylene Glycol Production, CHEMICAL ENGINEERING.
b. Intratec Solutions, 14th Sep 2023, Ethylene Glycol from Ethylene (Carbonation without EO By-Product) | Economic Analysis, Medium. - Shell, MASTER (EO/EG) Process (accessed 29th Apr 2024).

No Services yet available.
Enquire in Solutions how we can help you.
Content provided by
- Updated by
-
 Kokel, Nicolas
- Updated
- 10/12/2024 6:59 AM
- Added by
-
 Kokel, Nicolas
- Added
- 12/1/2021 6:12 AM
Join ppPLUS to add new content, update or comment.