ppPLUS: Technologies and more
Go to Homepage to browse companies and process data
ppPLUS-Solutions providing Services and Support
Register creating your own models
Technology
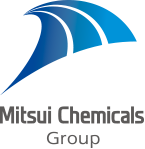
- Name
- Mitsui CX
- Owner
-
/ Mitsui Chemicals - Brand
- CX
- Process
- Polyethylene processes
- Type
- Stirred Tank Reactor Slurry Polymerization of Ethylene
- Available
-
Process capabilities
The CX Process is a low-pressure slurry process that produces high-density polyethylene (HDPE) and medium-density polyethylene (MDPE)[1].
The CX Process combines two Continuously Stirred Tank Reactors (CSTRs) connected in series. Polymerisation occurs in slurry with hexane used as a diluant and products with bimodal molecular-weight distribution (MWD) are produced. Here, bimodal polymer generally refers to two or more polymer types in one product obtained by polymerising two different polymers in sequence in each of the two reactors operating in a cascade. Both molecular weight distribution and comonomer distribution can be adjusted by separately adapting the operating conditions such as operating temperature and operating pressure in each of the two reactors without changing the catalyst[1,2].
This process combines a sophisticated polymerization process and innovative catalyst chemistry to make products with a wide melt-index range. The versatile catalyst and simple polymerization operation enable easy product changeover, reducing transition times and generating negligible off -spec during the conversion process. Mitsui has developed a new catalyst that contributes to improving the morphology of the polymer powder and enhancing ethylene conversion[1].
Processing Steps
- Ethylene, hydrogen, co-monomer (1-butene), and an ultra-high activity catalyst are fed to the reactor, and a polymerization reaction occurs in a slurry state.
- The slurry from the reactor is fed to the separation system.
- The wet cake made from slurry in the separation system is dried into powder in the dryer system.
- The solvent is separated from the slurry, and up to 90% of the separated solvent is recycled to the reactor without undergoing any treatment.
- The dry polymer powder is mixed with a stabilizer supplied in a pelletizing system and made into pellets[1].
- In CX process, emission of Volatile Organic Compounds (VOC) occur in the dryer system; VOCs are sent to the flare so that there are no emissions of VOC into the atmosphere[3].
Products
- A wide range of homopolymers and copolymers can be produced, including PE-100+ pipe grade.
- Melt indes: 0.01 ~ 50+.
- Molecular weight distribution & comonomer distribution: freely adjustable from narrow to wide range.
- Density: 0.93 ~ 0.97 g/cm3 [1]
Economics
Typical consumption per metric tonne of natural HDPE pellets:
Installed Capacity
With more than 40 years of licensing experience, Mitsunishi claims an installed base of 48 CX plants by 2019 with over 8 million tonnes of production per year corresponding to an 18% HDPE production market share[3]. Maximum plant capacity in 2019 is 500,000 tonnes per year.
References
- Seung Jae Yang, 9th Jul 2017, Mitsui Chemicals Inc., CX Process, High Density Polyethylene, Process License, Naver Blog.
- Big Chemical Encyclopedia, Mitsui CX Process
- Mitsui Chemicals, Technology Licensing, Polymer Technologies, 1. HDPE (CX Process): Bimodal slurry phase process to produce high quality HMW-HDPE for ultra-thin film, small & large blow molding and gas/water pipes including PE-100

No Services yet available.
Enquire in Solutions how we can help you.
Technology Unit |
---|
Catalyst Tank |
CSTR |
Dryer Unit |
Flare |
Intermediate Tank |
Pelletizer |
Solvent Recovery |
Storage Silo |
Entity | Site (Country) | Asset (Plant) | |||
---|---|---|---|---|---|
![]() |
![]() |
|
PE Slurry Process 1 | ||
![]() |
![]() |
|
PE Slurry Process 2 | ||
![]() |
![]() |
|
HDPE Polyethylene | ||
![]() |
![]() |
|
HDPE Plant | ||
![]() |
![]() |
|
HDPE Plant | ||
![]() |
![]() |
|
HDPE Plant | ||
![]() |
![]() |
|
HDPE Plant | ||
![]() |
![]() |
|
HDPE Unit |
Content provided by
- Updated by
-
 Kokel, Nicolas
- Updated
- 5/8/2024 7:22 PM
- Added by
-
 Kokel, Nicolas
- Added
- 1/11/2021 10:56 PM
Join ppPLUS to add new content, update or comment.