ppPLUS: Technologies and more
Go to Homepage to browse companies and process data
ppPLUS-Solutions providing Services and Support
Register creating your own models
Technology
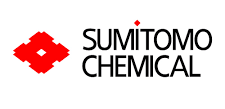
- Name
- Sumitomo POC
- Owner
-
/ Sumitomo Chemical Company, Limited - Brand
- Propylene Oxide by Cumene Process
- Process
- Oxidation
- Type
- Propylene Oxide via the Organic Peroxide Method
- Available
-
Sumitomo Chemical has developed a proprietary cumene-based propylene oxide (PO-only) process, often referred to as the Cumene Method or POC (Propylene Oxide by Cumene) Process. Unlike traditional organic hydroperoxide methods (such as PO-SM or PO/TBA), this technology produces PO without generating co-products like styrene monomer (SM) or tert-butanol (TBA).
Key Steps
1. Cumene Oxidation
- Feedstock: Cumene (isopropylbenzene) is oxidized with air to form cumene hydroperoxide (CMHP).
- This step is conducted under mild conditions, leveraging cumene’s stability and recyclability.
2. Epoxidation
- Reaction: CMHP reacts with propylene in the presence of a proprietary titanium-silica catalyst developed by Sumitomo.
- Products: The reaction yields propylene oxide (PO) and α,α-dimethylbenzyl alcohol (DMBA) also known as α-cumyl alcohol (CMA).
- Catalysts: The catalyst’s mesoporous structure enables high activity and selectivity, overcoming the limitations of conventional TS-1 zeolites for large molecules like CMHP.
3. Hydrogenation
- DMBA Conversion: The DMBA by-product is hydrogenated back to cumene, which is recycled to the oxidation step.
- This closed-loop ensures minimal waste and maximizes atom efficiency.
Figure 1 - POC process reaction cycle
POC Process Flow
The POC process comprises three major sections: (1) Product Formation; (2) Product Purification; and (3) Cumene Recovery.
(1) Product Formation. Fresh and recovered cumene is fed, along with air, to column reactors, where an oxidation reaction takes place. A sodium carbonate solution is also fed to the reaction media to control pH. The cumene hydroperoxide (CHP) effluent is routed to a separator vessel, where the carbonate solution is removed, and dissolved air is flashed off. The CHP is concentrated in an evaporator, and directed to the epoxidation reactor, where it reacts with fresh and recovered polymer grade (PG) propylene, yielding propylene oxide (PO) and dimethyl benzyl alcohol (DMBA). The epoxidation effluent is separated in a liquid and a gaseous stream in a flash vessel, which are sent to the Depropenizer columns.
(2) Product Purification. The liquid and gaseous epoxidation effluents are fed to low-pressure and high-pressure distillation columns, respectively. Propylene, propane and light ends are removed as overheads products from these columns. The C3’s stream from the high-pressure column is routed to the Propane Splitter, which separates propylene from propane, which is burned as fuel. The propylene is mixed with the overhead stream from the low-pressure column and returned to the Epoxidation reactor. The bottom products of the columns are mixed and routed to Crude PO Separation, where PO is separated from unreacted cumene and DMBA, which are directed to cumene recovery. The PO is further purified in PO
purification and PO product column, obtaining a 99.9 wt% PO.(3) Cumene Recovery. The bottom of PO crude separation is fed to cumene recycle column, which separates cumene, recycled to Peroxidation, from DMBA, which is sent to purification, yielding high purity DMBA, that is then is directed to a hydrogenolysis reactor. In this step, DMBA reacts with hydrogen, generating cumene, which is sent to purification and then recycled to Epoxidation.
Figure 2 - POC Process Schematic Diagram
Legend: 1. Oxidation, 2. Concentration, 3. Epoxidation, 4. Depropanizer, 5. Propane splitter, 6. Crude PO separation, 7. PO purification, 8. PO column, 9. Cumene recycle column, 10. DMBA purification, 11. Hydrogenolysis, 12. Cumene recoveryProcess Features
- No Co-Product Dependency: Unlike PO-SM/SMPO (which produces SM) or PO/TBA (which produces TBA/MTBE), the only significant product is PO. This eliminates market risks associated with co-product sales.
- Energy Efficiency: Cumene is used both as a reactant and solvent, simplifying recovery and reducing energy consumption compared to processes requiring methanol or other solvents.
- Heat Integration: The process is designed for optimal heat recovery between steps, further lowering energy requirements.
- Environmental Performance: No chlorine or salt by-products are generated and the process achieves lower overall CO₂ emissions relative to traditional hydroperoxide or chlorohydrin processes.
Technical Innovations
- Catalyst Development: Sumitomoʼs proprietary titanium-silica catalyst with a mesoporous structure enables high activity for the epoxidation of propylene with CMHP, a significant advance over conventional catalysts.
- Concurrent Engineering: The process was rapidly scaled from laboratory to commercial plant by integrating R&D and engineering teams, shortening the development timeline to just four years.
Commercialization and Licensing
- First Commercialization: The process was first commercialized at Sumitomo Chemicalʼs Chiba Works in Japan.
- Global Adoption: It has been licensed to and successfully implemented by:
- Petro Rabigh (Saudi Arabia)
- S-OIL (South Korea, 300,000 t/y plant)
- PTT Global Chemical (Thailand, 200,000 t/y plant)
- Licensing Partnerships: Sumitomo has partnered with KBR for global technology licensing, expanding the reach of this PO-only technology.
References
- Sumitomo Propylene Oxide by Cumene (POC) Process - Sumitomo Chemical Technology Licensing
- Junpei T SUJI et al., Development of New Propylene Oxide Process, R&D Report SUMITOMO KAGAKU, vol. 2006-I.
- Sumitomo Chemical Co., Ltd., Development and Commercialization of a New Manufacturing Process for Propylene Oxide Utilizing Cumene Recycling, Sumitomo Chemical Co., Ltd., Japan Association for Chemical Innovation (JACI), JACI Textbook Award to Green and Sustainable Chemistry (GSC) , Awards No 8, Issued March 2024 (Japanese version issued March 2023)
- 2021 - Propylene Oxide Production from Propylene and Cumene - Report Propylene Oxide E51A Cost Analysis - United States - INTRATECH
- Nov 30, 2015 - News Release: Sumitomo Chemical to License PP and PO Production Technologies to S-OIL - Sumitomo Chemical
- Aug 31, 2017 - Sumitomo Chemical Licenses PO Production Technology for Petrochemical Project of Thailand's Largest Petrochemical and Refining Company - Sumitomo Chemical
- Success Stories: GC Oxirane Co., Ltd. - Flawless Market Entry with “GCO” Brand Prestige Using Trusted Sumitomo’s Propylene Oxide Cumene Technology - Sumitomo Chemical Technology Licensing
- Mary Bailey, Aug 19, 2019 - Sumitomo Chemical licenses PO process technology for BPCL’s new petrochemicals project - Chemical Engineering
- May 22, 2024 - Press Release: KBR and Sumitomo Chemical Form Technology Licensing Alliance for Sustainable Propylene Oxide Production - KBR

No Services yet available.
Enquire in Solutions how we can help you.
Content provided by
- Updated by
-
 Kokel, Nicolas
- Updated
- 7/14/2025 5:54 PM
- Added by
-
 Kokel, Nicolas
- Added
- 7/11/2025 2:13 PM
Join ppPLUS to add new content, update or comment.