ppPLUS: Technologies and more
Go to Homepage to browse companies and process data
ppPLUS-Solutions providing Services and Support
Register creating your own models
Technology
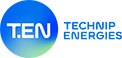
- Name
- Badger Cumene
- Owner
-
/ Technip Energies NV - Brand
- Badger Cumene Technology
- Process
- Alkylation
- Type
- Alkylation of Aromatic Compounds
- Available
-
Process History
The Badger Cumene process was commercialized in 1996, following years of collaboration between Badger Licensing and ExxonMobil in zeolite catalyst and process development. This technology marked a significant leap over older aluminum chloride and solid phosphoric acid processes, offering superior yields, energy efficiency, and environmental performance thanks to proprietary ExxonMobil zeolite catalysts. As of 2024, over 37 plants worldwide use the Badger Cumene process, accounting for more than half of global cumene capacity the technology partners are claiming.
Role of the Technology Partners
- Technip Energies, through its Badger Licensing partnership with ExxonMobil, serves as the global licensor and engineering partner for the Badger Cumene process. Technip provides technology licensing, process design, engineering services, technical support, and start-up assistance for new and revamped cumene plants.
- ExxonMobil supplies the proprietary zeolite catalysts and collaborates on continuous process improvements.
Process Summary
The Badger Cumene process is a liquid-phase alkylation technology for producing cumene (isopropylbenzene) by reacting benzene with propylene in the presence of a proprietary zeolite catalyst. The process is organized into three main sections: alkylation, transalkylation, and purification. In the alkylation reactor, benzene and propylene react to form cumene with extremely high selectivity. Byproducts such as polyisopropylbenzenes (PIPB) are converted back to cumene in a transalkylation reactor. The final purification section uses distillation to recover high-purity cumene, recycle unreacted benzene, and remove heavies. The process is known for its high efficiency, low benzene-to-propylene ratios, minimal byproduct formation, long catalyst life, and reduced environmental impact, making it ideal for integration with downstream phenol and acetone production.
Detailed Process Description
The Badger process is based on liquid-phase alkylation of benzene with propylene using proprietary ExxonMobil zeolite catalysts (notably the MCM-22 family). The process is typically organized into three main sections: alkylation, transalkylation, and purification.
- Alkylation:
Following feed preparation, benzene and propylene are introduced into a fixed-bed alkylation reactor system, where propylene is almost completely converted to cumene (>99.999% conversion). The reaction is exothermic and staged with intermediate cooling to manage temperature. A small fraction of cumene undergoes further alkylation to form polyisopropylbenzenes (PIPB).
- Transalkylation:
The PIPB byproducts are separated and reacted with additional benzene in a single-bed transalkylation reactor, also operating in the liquid phase. This step efficiently converts PIPB back to cumene, maximizing overall yield.
- Purification:
The process employs a simple, highly energy-efficient distillation train to:- Recover excess benzene as the overhead of the benzene recovery column and recycle it to the reactors,
- Isolate high-purity cumene product as the overhead of the cumene product column (typically >99.97% purity),
- Recover and recycle PIPB to the transalkylation section.
- Final purification and residue removal.
Process Efficiency
- Feedstock flexibility:
The Badger process can utilize propylene from various sources, including polymer grade, chemical grade, and refinery grade, offering flexibility in feedstock selection.
- Yield:
The Badger process achieves ultra-high yields, with cumene yield losses typically less than 0.3% of total raw materials consumed.
- Product Purity:
Regularly delivers cumene purity above 99.97% by weight.
- Energy Efficiency:
The process is highly energy efficient, with low benzene-to-propylene (B/P) and benzene-to-PIPB ratios. This allows for smaller reactors, reduced distillation loads, and lower utility consumption. Most of the exothermic heat of reaction is recovered, further reducing energy requirements.
- Catalyst Performance:
- The catalyst is free-flowing before and after use, requires no special packaging or handling, and is typically regenerated offsite due to its long cycle length.
- The ExxonMobil zeolite catalysts are non-corrosive, environmentally inert, and regenerable, with cycle lengths often exceeding two years and total lifespans of up to five years.
- Operating Conditions:
The process operates at moderate temperatures and pressures, enabling the use of carbon steel construction and minimizing capital costs.
- Operating Simplicity:
Carbon steel construction is possible due to non-corrosive catalysts, reducing capital costs.
Commercial Experience
The Badger Cumene process is the most widely adopted technology for cumene production worldwide according to the technology partners claiming that, as of 2024, it accounts for over half of global cumene capacity, with more than 12 million metric tons per year produced using this process and over 37 licensed units globally. Single train capacities as large as 750 KTA have been licensed and demonstrated, highlighting the scalability of the technology.
Note
- All major technical and commercial claims in the above article are documented in the licensor sources 1. to 6.
- Independent academic and technical literature confirms the process structure, catalyst properties, efficiency, and market dominance of zeolite-based cumene processes, including the Badger process.
- Exact commercial numbers and proprietary catalyst details are only available from licensor sources 7. to 14., but the general performance and advantages are well-supported by independent reviews and scientific articles.
References
- baderlicensing.com, Technip Energies, 2021, Badger Cumene technology flysheet.
- baderlicensing.com, Cumene Technology page.
- ten.com, Technip Energies, 2021, Phenolics brochure.
- baderlicensing.com, Badger, 2024, Phenolics Brochure.
- badgerlicensing.com, Badger, 2024, Badger Cumene Technology flysheet.
- ten.com, Technip Energies, Cumene Flysheet page.
- Shyh-Yuang Hwang et al., US 8,445,738 B2, Priority date: 23rd Sep 2009, Process for Producing Cumene, Assignee: Badger Licensing LLC.
- Thoms F. Degnan et al., Alkylation of aromatics with ethylene and propylene: recent developments in commercial processes, Applied Catalysis A: General 221 (2001), DOI: 10.1016/S0926-860X(01)00807-9.
- U.S. Department of Energy (DOE) Office of Scientific and Technical Information (OSTI), 24th Feb 1993, Mobil/Badger to market zeolite-based cumene technology.
- S.A. Zarutskii et al., Simulation of the Process for Cumene Production by Alkylation of Benzene in Equilibrium Reactor, Petroleum Chemistry, vol. 58, no. 8, Aug. 2018, pp. 681-686.
- Marcus Ceasar, PEP Process Module, 8th Oct 1999, THE PRODUCTION OF CUMENE USING Zeolite CATALYST, Aspen Model Documentation.
- Jiquan Fu and Chuenhua Ding, Study on alkylation of benzene with propylene over MCM-22 zeolite catalyst by in situ IR, Catalysis Communications, Vol. 6, No. 12, pp. 770-776, 2005, ISSN 1566-7367, DOI: 10.1016/j.catcom.2005.07.011.
- R. Thakur t al., SYNTHESIS OF CUMENE BY TRANSALKYLATION OVER MODIFIED BETA ZEOLITE: A KINETIC STUDY, Brazilian Journal of Chemical Engineering, Vol. 33, No. 04, pp. 957 - 967, Oct - Dec 2016, ISSN 0104-6632, DOI: 10.1590/0104-6632.20160334s20150333.
- Vivek Gera et al., 16th Jan 2013, Economic Plantwide Control of the Cumene Process, Ind. Eng. Chem. Res. 2013, 52, 2, 830–846, ISSN 0888-5885, DOI: 10.1021/ie301386h.

No Services yet available.
Enquire in Solutions how we can help you.
Content provided by
- Updated by
-
 Kokel, Nicolas
- Updated
- 7/4/2025 7:59 AM
- Added by
-
 Kokel, Nicolas
- Added
- 7/3/2025 5:14 PM
Join ppPLUS to add new content, update or comment.