ppPLUS: Technologies and more
Go to Homepage to browse companies and process data
ppPLUS-Solutions providing Services and Support
Register creating your own models
Technology
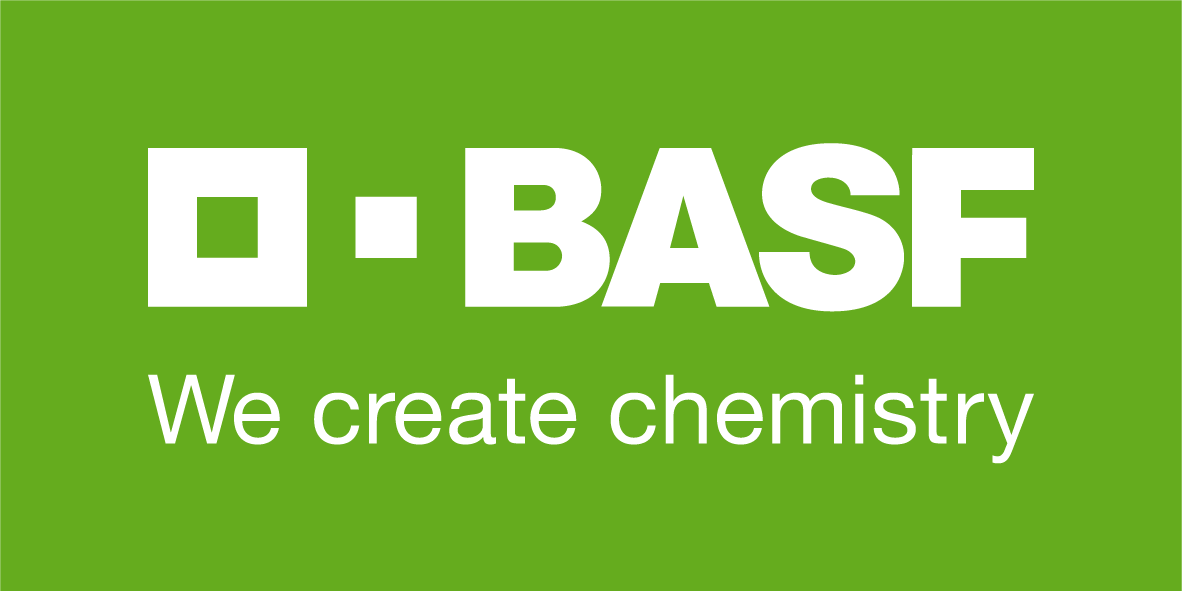
- Name
- BASF BDE
- Owner
-
/ BASF SE - Brand
- BASF Butadiene Extraction Technology
- Process
- Olefin processes
- Type
- Butadiene Extraction
- Available
-
Introduction
To produce High-Purity Butadiene (BD) from a Mixed C4 Stream, typically a Byproduct Stream from an Ethylene Plant using Liquid Feeds (Liquids Cracker). The BASF process uses n-Methylpyrrolidone (NMP) as the solvent with typically more than 98% of the 1,3-Butadiene contained in the Mixed C4 Feed recovered as product.
Process Overview
1,3-Butadiene is recovered from a C4 cut by extractive distillation using aqueous N-Methylpyrrolidone (NMP) as selective solvent. NMP substantially improves the relative volatilities of the components and prevents the formation of azeotropes. While the bulk of accompanying C4 hydrocarbons are separated from 1,3-butadiene by extractive distillation certain light and heavy components are separated by conventional distillation.
Different process configurations are available so that the process can be designed to suit the specific requirements of the project as shown in Fig. 1 and Fig. 2.
The Butadiene Extraction Unit typically comprises the following sections:
- Propyne Separation (Front or Tail End)
- Extractive Distillation (2 stages)
- Degassing
- Butadiene Distillation
- Solvent Regeneration
Figure 1 - BASF BDE-Process: Standard Configuration (Option 1).
Figure 2 - BASF BDE-Process: Standard Configuration (Option 2).
Propyne Separation
The C4 cut from Battery Limits enters the Pre-Distillation Tower, in which Propyne, Propadiene and other light components are separated as gaseous overhead product.
Extractive Distillation
Its bottom product will be evaporated and fed into the bottom section of the Main Washer. The solvent (NMP containing approx. 8 % by weight of water) enters the column a few trays below the top, absorbing butadiene and part of the butenes in counter-current flow. At the top of the column, the raffinate consisting of butanes and butenes is drawn off. Traces of solvent in the raffinate vapors are washed out by reflux.
The solvent loaded with butadiene and some butenes is drawn off at the bottom of the Main Washer and passed onto the top of the Rectifier. A vertical plate, which is installed in the upper section of the Rectifier separates the first extraction stage (first compartment) from the second extraction stage (second compartment). In the first compartment the less soluble, i.e. more volatile butenes are stripped from the solvent. The gaseous mixture of butadiene and butenes withdrawn from the top is recycled to the bottom of the Main Washer.
The butadiene vapors rising from the Rectifier lower section enter the second compartment and are routed in counter-current to fresh solvent. The C4 acetylenes are separated from the 1,3-Butadiene due to their lower vapor pressure in NMP. Crude 1,3-Butadiene is drawn off as overhead product. Traces of solvent are separated by reflux.
Degassing
The solvent collected in the Rectifier bottom is heated up and flashed into a separate bottom compartment before it is sent to the Degassing Tower. Here, the solvent is completely stripped from hydrocarbons using solvent and water-containing vapor generated by a steam-heated reboiler. The C4 acetylenes diluted with water vapor and 1,3-Butadiene are drawn off as a side stream of the Degassing Tower and enter the Acetylene Washer where remaining NMP is separated by condensate reflux.
The energy of the hot stripped solvent drawn off from the bottom of the Degassing Tower is recovered by heat integration. The solvent is cooled and recycled to the extractive distillation section.
The overhead vapors of the Degassing Tower enter the recycle gas compressor and are sent to the bottom section of the Rectifier.
Distillation
The crude butadiene from the top of the Rectifier’s second compartment is fed into the Butadiene Distillation Column. In its top section, water and a bleed stream comprising remaining light components are separated from butadiene product. A small stream containing heavy ends is drawn off as bottom product. The butadiene product is withdrawn as liquid side product.
Solvent Regeneration
For regeneration of the solvent, a small bleed of stripped solvent is continuously drawn off, distilled in a stirred vessel under vacuum and recycled to the process. When the residue in the stirred vessel rises to such extent that the heat transfer decreases, the solvent supply is stopped and the residue is discharged as waste.
Product Yields
Butadiene
The process provides a high yield (>98%) of particularly high purity (>99.7%) butadiene.
By-Products
The by-products below are usually recycled to the cracker:
- C4 acetylene stream
- C3/C4 hydrocarbons
- C4/C5+ hydrocarbons
Regeneration Residue
The viscous residue discharged discontinuously from the solvent regeneration is usually incinerated. Approximately 6 batches/year of 1–2 tons for a 100 kta Butadiene Unit.
Process Waste Water
The process waste water is usually treated in the waste water facilities of the petrochemical complex. Approximate flow is 0.5 m3/hr for a 100 kta Butadiene Unit.
Utility Consumption
Typical utility consumption per ton of Butadiene product:
- electrical power: 150 kWh/t
- steam (10 bar g): 1.7 t/t
- cooling water Δt = 7 °C: 150 m3/t
- NMP make up: 0.20 kg/t
Required Plant Area
The required area for a 100 kta unit is approximately 35 x 74 m (will be adapted to actual requirements).
References
- Introduction: Bee, 5th Jun 2018, 1,3-Butadiene (Extraction from mixed C4) Process by BASF/Lummus Technology, Hydrocarbon Process Engineering Info
- Description: Air Liquide Lurgi, 29th Mar 2010, Butadiene Extraction | BASF NMP Process, Document 311e/03.10/5
- BASF, BASF Butadiene Extraction Technology.

No Services yet available.
Enquire in Solutions how we can help you.
Entity | Site (Country) | Asset (Plant) | |||
---|---|---|---|---|---|
![]() |
![]() |
|
Butadiene Plant | ||
![]() |
![]() |
|
BD Plant | ||
![]() |
![]() |
|
BD Plant | ||
![]() |
![]() |
|
Butadiene Extraction | ||
![]() |
![]() |
|
BD Extraction | ||
![]() |
![]() |
|
BD Plant | ||
![]() |
![]() |
|
BDEU |
Data provided by
- Updated by
-
 Kokel, Nicolas
- Updated
- 6/27/2024 6:51 AM
- Added by
-
 Kokel, Nicolas
- Added
- 3/26/2021 12:00 AM
Join ppPLUS to add new content, update or comment.