ppPLUS: Technologies and more
Go to Homepage to browse companies and process data
ppPLUS-Solutions providing Services and Support
Register creating your own models
Technology
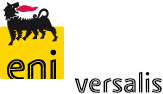
- Name
- Versalis Ethylbenzene
- Owner
-
/ Versalis S.p.A. - Brand
- Versalis Ethylbenzene Production Technology
- Process
- Alkylation
- Type
- Alkylation of Aromatic Compounds
- Available
-
Process Summary
Versalis Ethylbenzene production technology is based on the proprietary, highly selective and stable zeolite-based catalysts PBE-1 for alkylation and PBE-2 for transalkylation stages. The first industrial PBE catalyst drop in case started operations in 2001.
Process Description
- The fresh benzene feeds a pre-treatment section, where a guard bed is used to remove harmful impurities (catalyst poisons).
- Then, treated benzene enters in the distillation section where it is pumped to the reaction sections with recycled benzene.
- In the alkylation section, the reaction of ethylene with benzene takes place in liquid phase in one or more fixed bed reactors with multibed arrangement.
- Due to reaction exotermicity, external intra-bed refrigerators are required, with complete heat recovery.
- The alkylation effluent, which consists mainly of unconverted benzene, ethylbenzene, diethylbenzene and other by products feeds the distillation section.
- In the transalkylation section, the diethylbenzene produced in the alkylation and separated in the distillation section reacts with excess benzene to produce additional EB. The benzene/diethyl benzene mixture is first preheated and then sent to a dedicated fixed bed reactor, where the isothermal reaction takes place in liquid phase.
- The transalkylation effluent, which consists mainly of ethylbenzene, unreacted benzene and diethyl benzenes, and by-products such as diphenilethanes, feeds the distillation section. The distillation consists of a 3-column train.
- From the first one, the benzene is removed from the top to be recycled back to reaction sections.
- From the top of the second column is separated pure EB.
- In the third column, operated under vacuum, the separation of heavier by-products is carried out. Transalkylable polyethyl benzenes (mainly diethylbenzene) are removed from the top of the column, while high boiling by-products (Flux oil) are extracted from the bottom.
Key Features
Product Quality Ethylbenzene 99.98 wt % Di-ethylbenzene < 5 ppm max Xylenes almost nil Main Process Parameters Material Balance tonne per tonne Ethylbenzene Benzene 0.738 Ethylene 0.265 Utilities Consumption per tonne Ethylbenzene Net Steam Consumption -0.3 tonnes Key features of Versalis EB production technology are:
- proprietary, non-corrosive and extremely tolerant to poison PBE-1/2 zeolite based catalyst;
- ultra high product purity (typical value 99.98%);
- 100% ethylene conversion and overall 99.7% yield throughout the whole run length;
- negligible amount of xylenes by-produced (less than 10 ppm);
- simple and safe operation;
- all carbon steel construction and no critical proprietary equipment that have to be supplied by the licensor;
- low investment and plant maintenance costs;
- environmentally friendly proprietary zeolite catalyst. Easy catalyst handling and spent catalyst disposal;
- stable catalyst;
- continuous run-length betweenregenerations from 2 to 7 years;
- extended catalyst life (up to 5 reaction/regeneration cycles without performance deterioration);
- efficient and reliable fresh benzene treatment to protect the catalyst from nitrogen contaminants;
- low environmental impact;
- no acid waste stream and minimal fugitive emissions.
PBE type catalysts
PBE type catalysts show very high selectivity for alkylation and transalkylation and, above all, a very high stability, at the highest level among common zeolite based catalysts. More particularly, the preparation procedures allow optimal values for extrazeolite porosity and degree of interconnectivity, which results in very high catalyst stability, with very low ethylene oligomerisation and deactivation due to coke deposition.
Waste and Emissions
The process produces no liquid wastes or vapour emissions with the exception of oily water and vacuum pumps vents. Spent catalyst can be regenerated several times and
at the end of its lifetime can be disposed in a normal landfill. The plant can be provided with a vent recovery network, for continuous and non-continuous vents, to be sent to a combustor in order to lower all the plant emissions to a practically negligible amount.Industrial applications
The first industrial Ethylbenzene plant was a PBE type catalyst drop in case which started the operations in 2001; a second grass-root Ethylbenzene unit of 650 kt/y has been licensed by and started-up in 2009 to feed a Styrene downstream plant.
References
- Versalis proprietary process technology, ETHYLBENZENE with PBE-1/2 Zeolite based proprietary catalyst, Document created 30th Jan 2019, modified 14th Nov 2022.

No Services yet available.
Enquire in Solutions how we can help you.
Content provided by
- Updated by
-
 Kokel, Nicolas
- Updated
- 4/20/2025 1:13 PM
- Added by
-
 Kokel, Nicolas
- Added
- 1/26/2025 7:19 AM
Join ppPLUS to add new content, update or comment.