ppPLUS: Technologies and more
Go to Homepage to browse companies and process data
ppPLUS-Solutions providing Services and Support
Register creating your own models
Technology
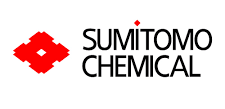
- Name
- Sumitomo PMMA
- Owner
-
/ Sumitomo Chemical Company, Limited - Brand
- PMMA Technology
- Process
- PMMA processes
- Type
- Bulk Polymerization of MMA
- Available
-
Process Summary
An apparatus and method for continuous polymerization can be used and applied to the production of a methacrylate-based polymer such as polymethyl methacrylate (PMMA). The method for continuous polymerization uses an apparatus for continuous polymerization which comprises:
- a reaction vessel 10;
- a means 20 for supplying a raw material monomer (monomer supply pump 20);to the reaction vessel 10;
- a means 25 for supplying a polymerization initiator (an initiator supply pump 25) to the reaction vessel 10;
- a means 31 for detecting a temperature (temperature sensor 31) in the reaction vessel 10;
- a means 15 for regulating a temperature of an outer wall surface (a jacket 15) of the reaction vessel 10 so as to have a preset temperature;
- a means 30 for controlling a supply flow rate (a control unit 30) of the raw material monomer and/or the polymerization initiator to the reaction vessel 10 by the monomer supply means and/or the initiator supply means so that the temperature in the reaction vessel becomes substantially the same temperature as the preset temperature of the temperature regulation means.
Process Flow Diagram
Other devices of the process according to illustration are:
- Monomer supply tank 21;
- Monomer supply route (piping) 23;
- Monomer heater/cooler 22;
- Monomer supply port 12;
- Initiator supply tank 26;
- Initiator heater/cooler 27;
- Initiator supply route (piping) 28;
- Agitating blade 11;
- Exhaust port 13;
- Polymerization syrup lead-out route 35 (monomer recovery tank 35);
Process details
- The state in the reaction vessel 10 is preferably made into an adiabatic state. The temperature in the reaction vessel 10 during a polymerization reaction is preferably set at approximately 120° C. to 180° C., preferably approximately 130° C. to 170° C.
- Flooded state in the reaction vessel 10 includes a method of discharge a polymerization syrup produced by a polymerization reaction out of the reaction vessel 10 through an exhaust port 13 placed on the uppermost portion of the reaction vessel 10. The pressure in the reaction vessel 10 may be approximately 10 to 20 kg/cm2.
- The average residence period of time of the raw material monomer in the reaction vessel 10 is more preferably about 20 minutes to about 1.5 hours. When the average residence period of time is more prolonged than required, the yield of oligomers such as a dimer and a trimer is increased to bring a possibility of lowering heat resistance of the resulting polymer product.
- The rate of polymerization is not particularly limited, and may be set at 40% by weight to 70% by weight. The higher rate of polymerization brings higher productivity of the polymer, while too much higher rate of polymerization may make the viscosity of a reaction system become so higher as to require greater agitation power. On the other hand, too much lower rate of polymerization may bring lower productivity of the polymer and greater load for recovering the unreacted raw material monomer.
- the raw material monomer separated and recovered from the polymerization syrup is stored in a monomer recovery tank 35 and then supplied to the monomer supply tank 21 again as required.
- With regard to the recovered raw material monomer, in order that a polymerization reaction may not progress while stored in the monomer recovery tank 35 and the monomer supply tank 21, it is preferred to make a polymerization inhibitor exist at a concentration of 2 ppm to 8 ppm, set the oxygen concentration of a gas phase portion at 2% by volume to 8% by volume and additionally store in a cooled state, for example, under a low temperature of approximately 0° C. to 5° C.
Polymerization Example
Polymethyl methacrylate was manufactured by continuous bulk polymerization:
- A complete mixing-type reaction vessel (internal capacity: 4.7 m3) equipped with a MIG blade (70 rotations per minute) as an agitating blade 11 and a jacket 15 for covering approximately the whole reaction vessel was used as a reaction vessel 10.
- A mixture containing 94.6% by weight of methyl methacrylate (MMA), 5.3% by weight of methacrylate (MA) and 0.08% by weight of a chain transfer agent (n-octyl mercaptan) was used as a raw material monomer supplied by a monomer supply means.
- A quintuple reciprocating pump was used for a monomer supply pump 20, of which supply flow rate was fixed at 9600 kg/h.
- A mixture containing 94.0% by weight of methyl methacrylate (MMA), 5.3% by weight of methacrylate (MA), 0.10% by weight of a chain transfer agent (n-octyl mercaptan) and 0.46% by weight of a polymerization initiator (1,1-di-tert-butyl peroxy-3,3,5-trimethylcyclohexane) was used as a polymerization initiator to be supplied by a polymerization initiator supply means.
- A triple reciprocating pump was used for an initiator supply pump 25. A supply flow rate thereof was set at 500 kg/h in starting polymerization, and thereafter was properly fluctuated by changing the output value of the pump depending on the temperature change in the reaction vessel.
References
- Kazuhiro Yamazaki, Akira Nishitani. Priority date 3rd Oct 2005; Status: expired. US7728081B2 assigned to Sumitomo Chemical Co Ltd. Apparatus for continuous polymerization and method for continuous polymerizing using the same.

No Services yet available.
Enquire in Solutions how we can help you.
Entity | Site (Country) | Asset (Plant) | |||
---|---|---|---|---|---|
![]() |
![]() |
|
PMMA Plant | ||
![]() |
![]() |
|
SMP-I | ||
![]() |
![]() |
|
SMP-II | ||
![]() |
![]() |
|
SMP-III |
Content provided by
- Updated by
-
 Kokel, Nicolas
- Updated
- 12/31/2024 5:01 PM
- Added by
-
 Kokel, Nicolas
- Added
- 3/20/2021 5:06 PM
Join ppPLUS to add new content, update or comment.