ppPLUS: Technologies and more
Go to Homepage to browse companies and process data
ppPLUS-Solutions providing Services and Support
Register creating your own models
Technology
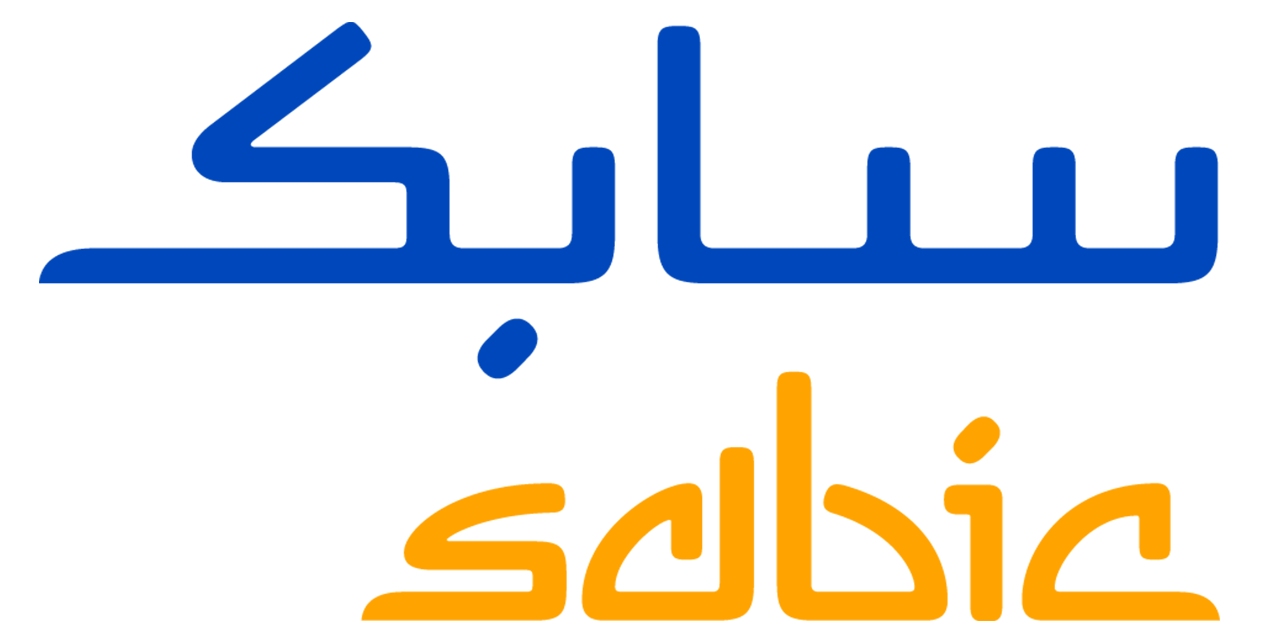
- Name
- SABIC CTR LDPE
- Owner
-
/ SABIC - Brand
- CTR LDPE technology
- Process
- Polyethylene processes
- Type
- High-Pressure Polymerization of Ethylene
- Available
-
Technology Summary
The Clean Tubular Reactor Technology (CTR®) is a non-pulsing technology where ethylene is polymerized through a radical reaction initiated by peroxides at a pressure of approximately 2500 bar in a tubular reactor. The reactor is a plug flow type reactor. Not all the ethylene is converted into polymer on the first pass. The unconverted monomer is recycled to the compression section and the produced LDPE, as a melt, is extruded[1].
Technology ownership
The Tubular Reactor Polymerisation of Ethylene technology was originally patented by STAMICARBON N.V. in Fe. 1967[2]. DSM started licensing CTR LDPE in 1995[3]. SABIC inherited the CTR LDPE Technology when it acquired DSM's petrochemicals business in 2022[4]. Today, Technip Energies is the exclusive licensing support contractor of SABIC for the Clean Tubular Reactor LDPE technology[1].
Features of the CTR® LDPE Technology
Claimed advantages of the CTR LDPE Technology are simplicity of design and operation resulting coupled with the so-called 'Clean Tubular Reactor' concept, resultiing in low investment cost, high on-stream times, high prime grade percentage and low manufacturing costs[1,2].
A conceptual Block Flow Diagram (Fig. 1) shows the low pressure cycle, the high pressure cycle, inputs and outputs of the process. The chain transfer agent is added to the booster compressor, ethylene in fed to the primary compressor and recycle is added between primary and secondary compressor stages. In particular, the initiator from cans is blended in minaral oil and the mix is injected via four initiator dosing systems at different points along the reactor lenght (Fig. 2)[2].
Figure 1 - Conceptual Block Flow Diagram of the CTR LDPE Technology[2].
The characteristics of the CTR LDPE Technology are as it follows[2]:
- Plug flow
- Design pressure: 3,000 bar
- Design temperature: 300°C
- Four reaction peaks
- Initiators: peroxide only
- Conversion: up to 38.5%
- No fouling
- No pressure pulsing required
Figure 2 - Initiators Injection Points along the CTR Tubular Reactor[2].
The CTR Reactor is claimed to be "Simple" in Design—by comparison with the "Complex" Design of competitor's reactors—resulting in a non-pulsating reactor as depicted in Fig. 3[2].
CTR reactor
- Uniform tube bore
- no direct cooling
- non bumping
- low peak temperature
- high cooling water temperature
- high initial temperature
- Pressure: ± 2,800 bar
Competitor's reactors
- Telescope reactor
- direct cooling
- bumping
- /
- low cooling water temperature
- low initial temperature
- Pressure: ≥ 3,000 bar
Figure 3 - Operating Temperature Profiles of the CTR Tubular Reactor[2].
Plant References
More than 10 plants are in operation and Eight references were designed by Technip Energies[1].
Literature
- Technip Energies, Oct 2023, Technip Energies Technology Handbook.
- STAMICARBON N.V. (NL), GB1196183 (A), Priority date 9th Feb 1967, Process for Preparing Ethylene Polymers or Copolymers.
- SABIC, May 2012, SABTEC CTR LDPE Technology, Global Petrochemicals conferennce, Cologne, German.
- Oil&Gas Journal, 3rd Apr 2002, SABIC to acquire DSM's petrochemicals business for almost $2 billion.

No Services yet available.
Enquire in Solutions how we can help you.
Entity | Site (Country) | Asset (Plant) | |||
---|---|---|---|---|---|
![]() |
![]() |
|
LDPE Plant | ||
![]() |
![]() |
|
PE Plant | ||
![]() |
![]() |
|
LDPE Plant | ||
![]() |
![]() |
|
LDPE-T | ||
![]() |
![]() |
|
LDPE Plant | ||
![]() |
![]() |
|
LDPE Plants | ||
![]() |
![]() |
|
LDPE Plant |
Data provided by
- Updated by
-
 Kokel, Nicolas
- Updated
- 8/8/2024 6:32 AM
- Added by
-
 Kokel, Nicolas
- Added
- 7/6/2024 9:01 AM
Join ppPLUS to add new content, update or comment.