ppPLUS: Technologies and more
Go to Homepage to browse companies and process data
ppPLUS-Solutions providing Services and Support
Register creating your own models
Technology
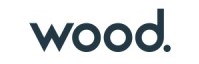
- Name
- Wood SYDEC
- Owner
-
/ John Wood Group PLC - Brand
- SYDEC
- Process
- Cracking
- Type
- Petroleum Coking
- Available
-
The Selective Yield DElayed Coking (SYDEC®) process is a technology that upgrades heavy hydrocarbons such as Residue/Tar to lighter Hydrocarbons.
Process Details
-
The heavy Hydrocarbon feed is preheated by recovering the heat of the partial recycle stream of Heavy Gas Oil, which is a product separated in the middle of the fractionator (1).
-
The pre-heated feed is fed to the bottom of the fractionator (1), where it is combined with the recycle components.
-
The combined feed mixture is supplied to the coker heater by the fractionator bottom pump, where it is heated to a coking temperature ranging from 480°C to 510°C. Partial vaporization and mild cracking occur during this heating process.
-
The resulting vapor-liquid mixture heated to the coking temperature is supplied to the coking drum (2) or (3) and cracked again.
-
Hydrocarbons from the overhead of the coking drum is supplied to the fractionator (1) and separated into Fuel Gas, Naphtha, Light Gas Oil and Heavy Gas Oil.
-
The separated Fuel Gas and Naphtha are supplied to the Vapor Recovery Unit (VRU) (4) and separated again into Dry Gas, C3/C4, and Naphtha.
At least two coking drums are installed since, while one of the coking drum is in coking mode (forming Coke on the inner wall of the coking drum), the other one is in decoking mode (removing the Coke formed on the inner wall of the coke drum). Decoking is the process of shooting a high-pressure Water jet from the top of a coking drum onto the coke formed on the coking drum wall and discharging the coke to the bottom of the cokinge drum.
In addition to the coking drum, the coking unit includes Coke handling, Coke cutting, Water recovery, and a blowdown system. Vent gas discharged from the blowdown system is supplied to the VRU (4).
Operating Conditions
A typical operating example of the SYDEC® process is as follows:
- Heater outlet temperature
- Coking drum pressure
- Recycle ratio (rel. to fresh feed)
480-510°C
1.03~6.9 barG
0~1.0As the coking temperature increases, the formation of Coke decreases and the formation of liquid Hydrocarbon and the end point of Gas Oil increase. Meanwhile, increasing coking drum pressure or recycling ratio increases the formation of Fuel Gas and Coke, while decreasing the formation of liquid Hydrocarbon and the end point of Gas Oil.
Yields
Typical product yields are shown in the following table:
Products, wt% Max. distillation Anode Coke Needle Coke Fuel Gas 8.7 8.4 0.8 Naphtha 14.0 21.6 8.4 Gas Oil 48.3 43.8 41.6 Coke 29.3 26.2 40.2 Economics
Utilities consumption per barrel of feed are as follows:
- Fuel
- Electricity
- Steam
- Cooling water
30,244 kcal
3 kWh
15.9 kg
0.136 m3Source: Naver blog, 9th Oct 2017, [UOP/Foster Wheeler] Selective Yield Delayed Coking (SYDEC®) Process
-

No Services yet available.
Enquire in Solutions how we can help you.
Entity | Site (Country) | Asset (Plant) | |||
---|---|---|---|---|---|
![]() |
![]() |
|
Delayed Coker | ||
![]() |
![]() |
|
Delayed Coker | ||
![]() |
![]() |
|
Delayed Coker |
Data provided by
- Updated by
-
 Kokel, Nicolas
- Updated
- 10/17/2024 7:14 AM
- Added by
-
 Kokel, Nicolas
- Added
- 6/22/2024 5:34 AM
Join ppPLUS to add new content, update or comment.