ppPLUS: Technologies and more
Go to Homepage to browse companies and process data
ppPLUS-Solutions providing Services and Support
Register creating your own models
Technology
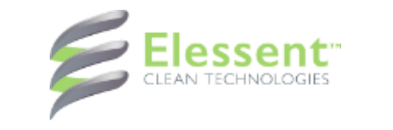
- Name
- Elessent STRATCO Alkylation
- Owner
-
/ Elessent Clean Technologies - Brand
- STRATCO® Alkylation Technology
- Process
- Fuel Processes
- Type
- Alkylation into High-Octane Alkylates
- Available
-
Technology History
A new company – Elessent Clean Technologies – has launched, as an international private equity consortium, consisting of BroadPeak Global LP, Asia Green Fund (AGF) and The Saudi Arabian Industrial Investments Company (Dussur), completed its transaction to purchase the Clean Technologies business of DuPont de Nemours, Inc. (Wilmington, Del.) on December 31, 2021.
The new, independent company has been named Elessent Clean Technologies and is a global leader in process technologies to drive sustainability and carbon neutrality in the metal, fertilizer, chemical and oil refining industries. Elessent retains exclusive rights to the technologies, expertise, products, and services to which these industries have grown accustomed from the Clean Technologies business over the years, including: MECS sulfuric acid and environmental technologies, BELCO® scrubbing technologies, STRATCO alkylation technology and IsoTherming hydroprocessing technology.
Technology Summary
The STRATCO® Alkylation Technology is a sulfuric acid catalyzed process that converts low-value, straight-chain olefins into high-value, branched components called alkylate. The technology combines propylene, butylenes and/or amylenes, either individually or as a mixture, with isobutane in the presence of sulfuric acid catalyst to produce high-octane, branched chained hydrocarbons for use in motor fuel and aviation gasoline.[2]
Technology Details
- Olefins and isobutane-rich streams along with a catalyst stream of sulfuric acid are charged to the STRATCO® Contactor™ reactor. The ratio of isobutane to olefins in the reaction zone must be maintained adequately high to prevent unfavourable olefin-to-olefin reactions from occurring that can result in low quality alkylate and higher acid consumption.[2]
Figure 1 - Alkylation reactor retrofit design
- The liquid contents of the Contactor™ reactor are circulated to create an optimized amount of interfacial area between the reacting hydrocarbons and the acid catalyst from the acid settler. This circulation ensures the entire volume of liquid in reactor is maintained at a uniform temperature.[2]
- The technology is effluent refrigerated to remove the heat of reaction using a refrigeration section consisting of a compressor and depropanizer to remove excess propane. Isobutane is flashed in the reaction zone to provide cooling for the reactors, which typically operate at around 45-60°F (7-15°C). This flashed isobutane is then compressed, condensed and cooled in the refrigeration section before being routed back to the reaction zone as refrigerant recycle, providing approximately one half of the isobutane required in the reaction zone.[2]
Figure 2 - Isobutane recycle streams
- The reactor products pass through a flash drum, are treated for removal of possible entrained sulfur species, and are fractionated in a deisobutanizer.
- The isobutane stream from the top of the deisobutaniser tower combines with the effluent refrigerant recycle to provide isobutane to the reaction zone and to promote the alkylation reaction. This stream makes up about one half of the total isobutane required for the reaction zone.
- The deisobutanizer bottoms are further fractionated into normal butane (if applicable) and whole alkylate products.[2]
Feed flexibility
- Segregation and processing of C3, C4 and C5 olefins without additional units upstream.
For example, Elessent started up the first ever commercial 100% isobutylene unit in 2019 at Hengli Petrochemical Company in Dalian, China.[2]
- Alkylation of non-traditional feedstocks.
For example, Elessent Clean Technologies was awarded the first ever and only license for the alkylation of a 100% amylene feedstock. Many operating STRATCO® alkylation units process some percentage of amylene olefins from the FCC, but this unit started up in the US Gulf Coast in 2019, and it is the first alkylation unit to process only amylenes.[2]
STRATCO® Contactor™ Reactor Technology
STRATCO® alkylation technology is offered with varying Contactor™ Reactor sizes to suit the smallest to the largest alkylation unit from a size 42 Contactor™ reactor for very small alkylation units to the size 74 Contactor™ reactor.[2]
Figure 3 - STRATCO® Contactor™ Reactor Main Connections
This reactor processes nearly doubles the volume of the more familiar size 63 Contactor™ reactor and offers a larger area for cooling per barrel of feed. The performance and resulting product quality and acid consumption of the size 74 Contactor™ reactor are the same as the size 63 but allows for better economy of scale. In addition, the STRATCO® XP2 technology is a Contactor™ reactor enhancement developed to improve the acid/hydrocarbon emulsion flow path near the tube bundle end of the Contactor™.[2]
Case Study
Table 1 - HF alkylation technology revamp, feed and product stream summary[2]
Olefin
feedIsobutane
feedPropane
feedn-Butane
feedAlkylate
productVolume flow, b/d 19,975 9,564 2,334 1,270 20,569 Composition, vol% Ethane
Propane
i-Butane
n-Butane
i-Pentane
n-Pentane
Propylene
Butylene
Amylene
C6+0.03
9.51
21.78
6.98
2.60
0.72
24.61
33.07
0.71
0.00
1.99
95.00
3.010.23
97.50
2.26
0.02
16.71
82.29
0.98
0.02
0.20
3.03
7.11
0.70
88.96
Commercial ExperienceOn 24th Dec 2024 (date accessed), Elessent is claiming that STRATCO® Alkylation Technology is the predominant sulfuric acid alkylation technology, holding 75% market share with approximately 80 STRATCO® effluent refrigerated alkylation units in commercial operation at refineries worldwide and with over 100 licensed units worldwide.[2]
The STRATCO® alkylation technology has commercial experience processing a wide range of alkylation feedstocks including FCC olefins, MTBE olefins, and large quantities of propylene, isobutylene, and amylene. Elessent has dozens of operating units worldwide processing an olefin feedstock from an FCC unit. A FCC mixed butylene feedstock is the most common feedstock to an alkylation unit. These feeds produce an alkylate product with a 96-97 RON depending on the amount of isobutylene present.[2]
Other commercial experience details[2]:- Units built in 1940s are still in operation
- Commercial alkylation units consistently make a 4‐ to 5-year turnaround plan cycle
- Unit successfully restarted after being shut down for 20 years
References
- Mary Bailey, 3rd Jan 2022, DuPont Clean Technologies rebrands as Elessent following acquisition, Chemical Engineering.
- Elessent Clean Technologies, STRATCO® Alkylation Technology page and information linked therein. (Accessed 24th Dec 2024)
- Olefins and isobutane-rich streams along with a catalyst stream of sulfuric acid are charged to the STRATCO® Contactor™ reactor. The ratio of isobutane to olefins in the reaction zone must be maintained adequately high to prevent unfavourable olefin-to-olefin reactions from occurring that can result in low quality alkylate and higher acid consumption.[2]

No Services yet available.
Enquire in Solutions how we can help you.
Technology Unit |
---|
B/D Drum |
Coalescer |
Compressor |
Depropanizer |
Drum |
Feed Dryer |
Heat Exchanger |
Isostripper |
K/O Drum |
Pump |
Reactor |
Scrubber |
Settler |
Entity | Site (Country) | Asset (Plant) | |||
---|---|---|---|---|---|
![]() |
![]() |
|
Alkylation Plant | ||
![]() |
![]() |
|
Alkylation Unit | ||
![]() |
![]() |
|
Alkylation Plant | ||
![]() |
![]() |
|
Alkylation Plant | ||
![]() |
![]() |
|
Alkylation Plant |
Data provided by
- Updated by
-
 Kokel, Nicolas
- Updated
- 6/21/2025 4:01 PM
- Added by
-
 Kokel, Nicolas
- Added
- 11/28/2022 4:25 PM
Join ppPLUS to add new content, update or comment.