ppPLUS: Technologies and more
Go to Homepage to browse companies and process data
ppPLUS-Solutions providing Services and Support
Register creating your own models
Technology
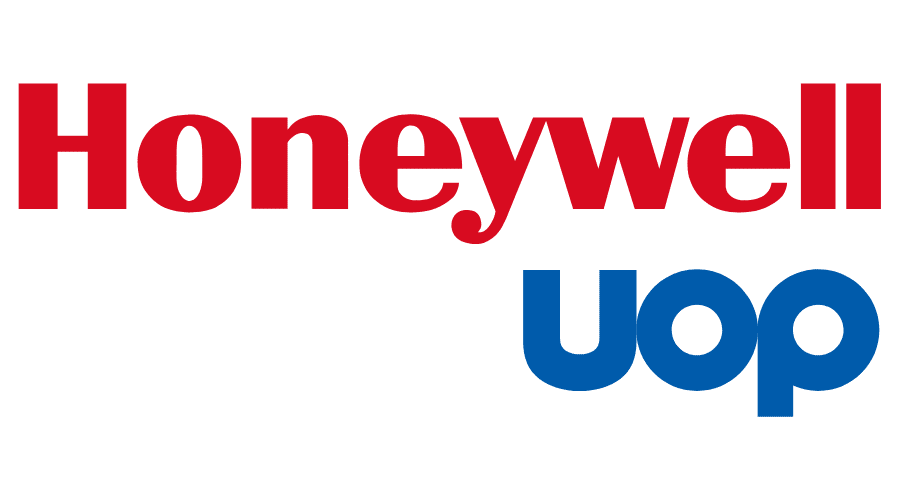
- Name
- UOP Unicracking
- Owner
-
/ Honeywell UOP - Brand
- Unicracking™
- Process
- Cracking
- Type
- Resid Hydrocracking
- Available
-
The UOP Unicracking™ process converts Heavier Feedstocks such as Vacuum Gasoil (VGO), De-asphalted Oil (DAO) or cracked feedstock from Bottoms Upgrading Units into Lighter Materials ranging from Liquid Petroleum Gas (LPG), Naphtha, Kerosene, Diesel or Unconverted Oil.[1]
The Process is carried out at moderate temperatures and pressures over a Fixed Catalyst Bed in which the Fresh Feed is cracked in a Hydrogen Atmosphere. Exact Process Conditions vary widely, depending on the Feedstock properties and the Products desired. However, pressures usually range between 35 and 219 kg/cm2 (500 and 3000 lb/in2 gage) and temperatures between 280 and 475°C (536 and 887°F).[2]
Different types of Unicracking™ Process Flows:[2]
- Single-Stage.
The Single-Stage Flow Scheme involves Full Conversion through Recycling of Unconverted Product and is the most widely used because of its efficient Design resulting in minimum cost for a Full-Conversion Operation. This Scheme can employ a Combination of Hydrotreating and Cracking Catalysts or simply Amorphous Cracking Catalysts depending on the Final Product required. - Once-Through
Unlike the Single-Stage Flow Scheme, the Once-Through Flow Scheme is a Partial Conversion Option that results in some yield of Unconverted Material. This Material is Highly Saturated and free of Feed Contaminants but is similar in molecular weight to the Feed. If a Refinery has a use for this Unconverted Product, such as FCC Feed or High-Quality Lube Base Oil, this Flow Scheme may be preferred. - Two-Stage.
In the Two-Stage Flow Scheme, Feedstock is treated and partially converted Once-Through across a First Reactor Section. Products from this Section are then separated by Fractionation. The Bottoms from the Fractionation step are sent to a Second Reactor Stage for Complete Conversion. This Flow Scheme is most widely used for Large Units where the Conversion in the Once-Through First Stage allows High Feed Rates without Parallel Reactor Trains and the added expense of Duplicate Equipment. - Separate-Hydrotreat.
The Separate-Hydrotreat Flow Scheme is similar to Single-Stage, but is configured to send Reactor Effluent that has been stripped of Hydrogen Sulfide and Ammonia to the Cracking Catalyst. This Configuration allows the Processing of Feedstocks with very high Contaminant levels or the use of Contaminant-Sensitive Catalysts in the Cracking Reactor if dictated by Product demands.
1. Ian Clarke, The Journey to Sustained Profitability: Maximizing Naphtha through the UOP Unicracking™Process, 2020 UOP LLC.
2. Hassan ElBanhawi, Hydrocracking Process
- Single-Stage.

No Services yet available.
Enquire in Solutions how we can help you.
Content provided by
- Updated by
-
 Kokel, Nicolas
- Updated
- 5/26/2025 8:49 AM
- Added by
-
 Kokel, Nicolas
- Added
- 11/19/2022 3:09 PM
Join ppPLUS to add new content, update or comment.