Site
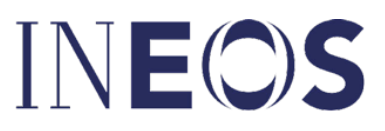
-
- Project One - Ethane Cracker Project
-
- INEOS Olefins Belgium NV
- Site in a Project-Phase
- Scheldelaan 480
-
Location of the PROJECT ONE project Area[1]
INEOS is constructing Project ONE, Europe's most sustainable ethane cracker plant in the Port of Antwerp, representing the largest investment in European chemistry in the past 25 years with a total cost of €4 billion. The project spans 55 hectares and will produce over 2 million tons of olefins (ethylene and propylene) annually[2].The construction is currently in full swing, with €3 billion already spent and approximately 1,700-1,800 workers on site, expected to peak at 2,500 workers in 202518. The project employs a modular construction approach, with massive components being shipped from specialized construction yards in Thailand, Abu Dhabi, and the Philippines[2].
In January 2025, the first two cracking furnaces arrived at the port, weighing 6,000 tonnes and standing 60 meters tall. These furnaces form the heart of the ethane cracker, where ethane will be converted to ethylene at high temperatures. The plant is scheduled for commissioning in 2026 and will create 450 permanent high-quality jobs[2].
The facility will produce essential chemical building blocks used in various applications, including lightweight materials for cars, lubricants for wind turbines, medical equipment, and sustainable packaging6. Notably, the plant's emissions will be less than half of the average of Europe's top 5 olefin plants[2].
Key Facts and Figures
CO2 Emissions[1]
- Project One produces ethylene with a carbon footprint of only 0.290 tonnes CO2-eq per tonne of HVC (High Value Chemical)
- Project One aims to become the first CO2-neutral cracker in Europe, convincingly to be completed in 10 years from the start of the cracker's operation via three possible CO2 emission reduction routes:
- Electrification of the furnaces using green electricity.
- Use of green hydrogen as fuel.
- Carbon Capture and Storage (CCS).
Logistics and Mobility[1]
Existing pipeline networks (Source: Flanders Investment & Trade / Port of Antwerp)
- The Project One site will be accessible to large ocean-going vessels and inland barges for the supply of ethane and other raw materials.
- Use will be made of the existing major pipeline networks in north-western Europe for ethylene and propylene.
Ethane Cracker[1]
Project One ethane cracker
The ethane cracker (ECR) will be one of the most innovative, efficient and sustainable cracking plants. in the world.. The ethane supplied will be converted into ethylene in the ethane cracker at a production capacity of 1 450 000 tonnes/year.
The cracking process consists of four process steps.
- In the furnace section, the actual conversion of ethane to ethylene takes place by bringing the ethane up to a high temperature in the presence of steam. This product flow is then cooled with water in the hot section. Additional steam is also formed in this step.
- Then, this flow is purified, for which it is first compressed.
- The compression stage provides the pressure needed for proper operation of the cold section, in which a first part of the compressed gases is purified.
- In the last section, the C3+ processing section, the heavier components are separated from each other. Finally, a number of local utilities support the process.
In the separation section, besides pure ethylene, pure propylene, C4 and C5+ hydrocarbons and pyrolysis oil are obtained as by-products from the cracking furnaces. In addition, propylene supplied from outside can be fed into this separation unit and purified so that this product can also be fed into the European pipeline network. Project One plans to produce 230 000 tonnes/year of pure (polymer grade) propylene in this way.
Supporting Utilities[1]
- Utilities Water
- Project One uses city water and demineralized water, both of which are piped to the site by utility companies. Rainwater is reused for sanitation and as cooling water. The use of demineralised water results in a significant reduction in water consumption and the amount of water discharged into the Scheldt.
- Independent cooling systems are provided for the ECR and supporting infrastructure. These systems remove the residual heat that cannot be reused from the various process parts. From an open system with forced airflow (cooling towers with fans), cooled water is pumped to the consumers. After use, the hot cooling water is returned to the cooling towers. Demineralised water is used in order to reduce the amount of fresh water needed and the purge flow from these cooling circuits.
- The waste stream is treated in
the water purification installation.
- Steam System
- in the furnace section, large amounts of superheated steam are generated at high pressure by recovering heat from the process gas. This steam is used internally to provide heat in various heat exchangers, drive machinery, and also to produce electricity.
- Two steam boilers will be installed to supply extra steam in situations where the plant's own steam production is reduced and/or the steam requirement is increased.
- Two steam turbines will be installed to generate electricity using the available steam.
- The condensed steam will be cleaned and returned to the steam boilers for reuse in the unit.
- Fuel Gas
- The fuel requirements of the ECR plant are met by using fuel gas. This is residual gas produced in the plant as a by-product. The fuel gas is rich in hydrogen and low in carbon.
- Part of the fuel gas produced is also used to regenerate the gas dryers.
- At times, when the quantity of available fuel gas is insufficient, natural gas can also be used temporarily.
- Storage
- The ethane is supplied as a liquid by ship at a very low temperature (-88.5˚C). From the ships this raw material is unloaded into a cryogenic tank and temporarily stored.
- In addition, there are also storage facilities for C3 and C4 co-products, C5+ co-products and pyrolysis oil.
- Various chemicals required for the processes, water treatment, etc. are also stored.
- Transport Infrastructure
- Loading installations will be provided for the loading of C3, C4, C5+ products and ethane transported by ship.
- The transport of the products and by-products (ethylene, propylene and C4 hydrocarbons) is almost entirely via existing pipelines.
- Truck loading areas are provided to transport products that occur in relatively limited quantities.
- Flares
- Flares are necessary to start up the installation, to release it for maintenance or to guarantee its safety in case of an incident.
- The project opted for the maximum use of ground flares. These are low flares with an enclosed flame:
- The system is designed so that ground flares are always activated first.
- one ground flare is provided for the ECR installation. This is used at start-up or when the plant is shut down for maintenance.
- a second ground flare is provided to protect the storage of gases (with a back-up ground flare for the latter to be used when the first is out of service for maintenance).
- a tower flare is also provided for the ECR that is only activated in the event of a major incident. These are situations in which, for safety reasons, a large quantity of gas needs to be evacuated at short notice. The tower flare is not used for normal start or stop procedures.
References
- INEOS, Project ONE, Environmental & Social Impact Assessment (ESIA).
- A.I. generated description, 15th Feb 2025, Claude 3.5 Sonnet.
System Info
- Modified by
-
 Kokel, Nicolas
- Modified
- 2/16/2025 6:33 AM
- Added by
-
 Braun, Uwe
- Added
- 5/23/2022 8:15 AM

No Services yet available.
Enquire in Solutions how we can help you.
Indicator | Unit | Value | |||
---|---|---|---|---|---|
![]() |
Modelling Status | True | 3 |
Site Settings
- Status
- A
- V
- P
Dashboard
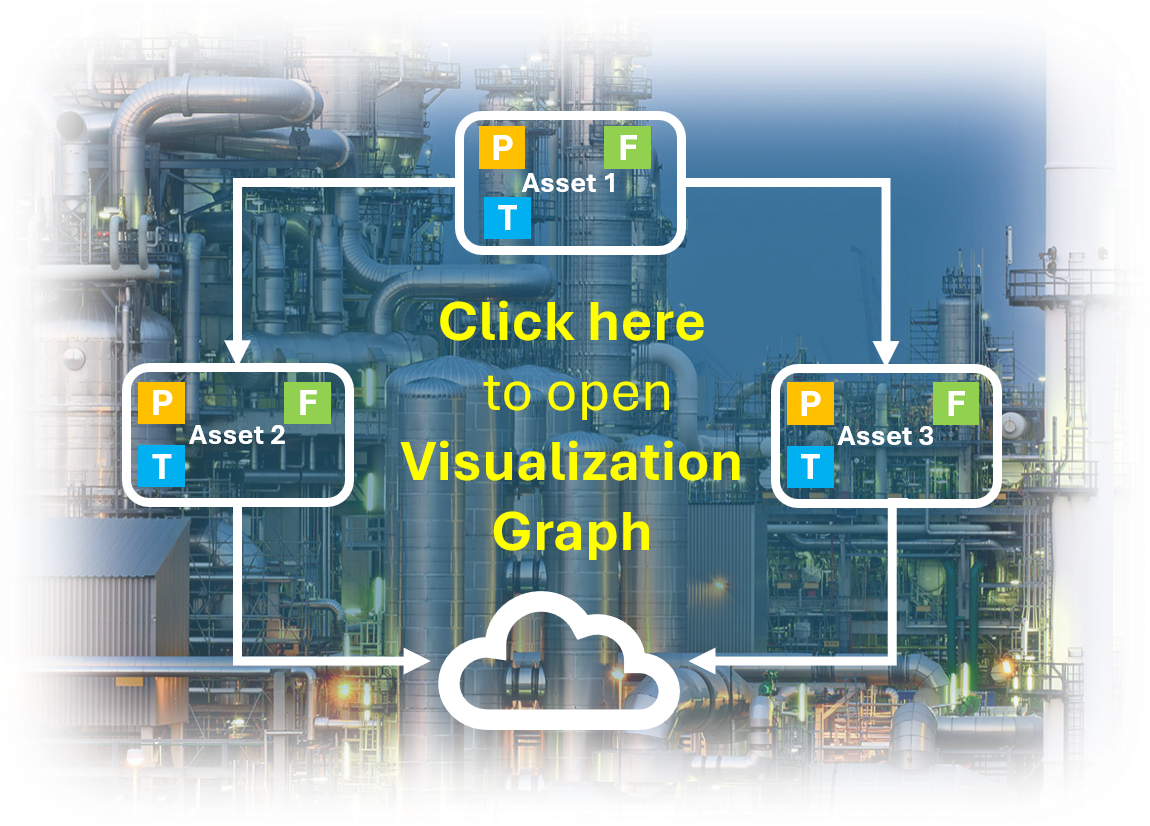
Please create Assets first to manage the Mass Balance Processes