Site
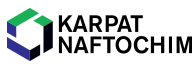
-
- Kalush Site
-
- Karpat Naftochim
- Predominantly Chemicals Operations
- 77306
-
/ Kalush - Ivano-Frankivsk
-
Olefins production plant
Plant capacity:
- 250,000 tpy of ethylene
- 117,052 tpy of propylene
- 101,166 tpy of benzene
Year of start-up – 1986.
Process developer: Company Linde, Germany.
Process technology description:- Feedstock for ethylene production are naphtha, acyclic hydrocarbons, LPG, butane cut and recycle cuts С2, С3, С4, С5.
- Polyolefin production plant comprises of:
- cracked gas pyrolysis, compression and separation department;
- hydrocarbons production department;
- hydrocarbons loading department.
- In October, 2005 a plant for С4/С5-cut hydrogenation with a capacity of 90 640 tpa was started-up, process developer is company Linde (Germany) under technology of AXENS (France). Investment volume amounted to 15 Mio. USD.
Principal products: ethylene, propylene, benzene. By-products: С4-cut, С5-cut, С9-cut, heavy pyrolysis resin.
Polyethylene production plant
Plant capacity:
- 100,000 tpy of polyethylene
- Year of start-up – 1997.
- Process developer: Company Union Carbide Corporation, USA
- Design: Company Linde, Germany.
Process technology description:
- Polyethylene production is based on gas-phase technology by license of company Union Carbide (USA).
- Polyethylene by gas-phase technology is obtained from ethylene and co-polymers in fluidized bed reactor using catalysts at low pressure.
- Ethylene from olefins plant is the main feedstock, hexane and butene are used as co-monomers.
- Using of co-monomers and catalysts enables to produce polyethylene grades with different properties and wide range of application.
Production process comprises of the following units:
- feedstock preparation and treatment;
- ethylene polymerization;
- polyethylene degassing;
- waste gas regeneration;
- polyethylene pelletizing;
- finished products warehousing and shipping.
Principal products: low-pressure polyethylene.
Vinylchloride production plant
Plant capacity: 300,000 tpy
Year of start-up: 1975 | 1996 – modernization
Design: company Uhde, GermanyProcess technology description:
- Vinylchloride production comprises of units for crude EDC production by means of direct ethylene chlorination and oxidative ethylene chlorination where hydrogen chloride obtained at pyrolysis is used in reactors with catalyst fluid bed.
- In the system of rectifying columns crude EDC is dehydrated and cleaned from “light” and “heavy” organochloride impurities.
- Rectified EDC obtained is subjected to high-temperature pyrolysis after which vinylchloride is isolated on rectification stage and EDC-recycle and hydrogen chloride are returned to the process.
- The process consists of two process lines of direct and oxi-chlorination, four pyrolysis furnaces and one process line for EDC and vinylchloride rectification.
Product:.vinylchloride monomer is used as a feedstock in S-PVC production.
Chlorine and caustic soda production unit
Plant capacity:
- 82,000 tpy of chlorine.
- 206,000 tpy of caustic soda
Year of start-up – 2010.
Process and design developer: company Uhde, Germany.Process technology of chlorine and caustic production by membrane method by Linde process consists of the following units :
- Salt unloading, treatment and storage.
- Brine preparation.
- Anolyte dechlorination.
- Chlorates dissolution.
- Sulphates removal.
- Electrolysis.
- Chlorine cooling and drying, sulphuric acid pre-concentration.
- Chlorine compression.
- Catholyte system.
- Caustic soda pre-concentration.
- Caustic soda storage, loading/unloading rack, caustic soda pumping house.
- Hydrogen compression and storage.
- Hydrochloric acid synthesis.
- Demineralized water preparation.
- Waste water neutralization.
- Waste gas dechlorination.
Principal products: caustic soda.
Suspension polyvinychloride production unit
Plant capacity: 300,000 tpy.
Year of start-up – 2011.
Process developer : Company Vinnolit, Germany.
Design: company Uhde, Germany.Production process technology consists of the following units:
- Cold and hot demineralized water storage;
- Fresh and recovery vinylchloride (VCM) and (R-VCM) storage;
- Chemicals dissolving and preparation;
- Vinylchloride polymerization (two parallel lines with two reactors in each.
- Polyvinychloride suspension degassing (two parallel lines).
- Unreacted vinylchloride recovery.
- Polyvinychloride suspension centrifuging and drying (two parallel lines).
- Finished products storage and bagging.
- Waste water treatment
- Demineralized water production unit.
- Cooling tower with a pump house.
Principal products: suspension polyvinyl chloride.
System Info
- Modified by
-
 Kokel, Nicolas
- Modified
- 5/14/2025 7:30 PM
- Added by
-
 Braun, Uwe
- Added
- 11/5/2024 10:33 AM

No Services yet available.
Enquire in Solutions how we can help you.
Indicator | Unit | Value | |||
---|---|---|---|---|---|
![]() |
Modelling Status | True | 2 |
Site Settings
- Status
- A
- V
- P
Please create Assets first to manage the Mass Balance Processes